Photo of the month – August 2015 |
[German version] |
Torpedo – A hazard for hazardous cargo
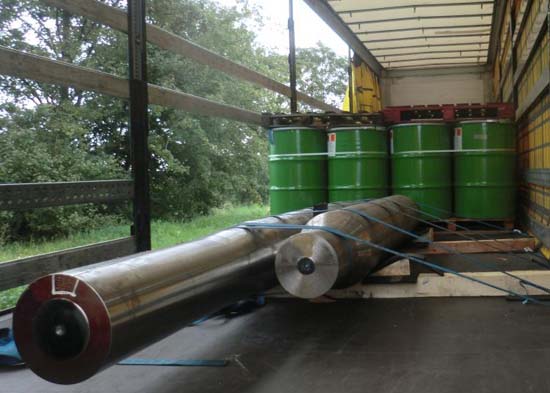
Figure 1 [Daniel Heyer]
At a first glance it might appear that all is well. We can see a truck loaded with long steel components, a few tie-down lashings and anti-slip mats – that could well be just fine. But as soon as we start really thinking about the way in which the load is secured, we notice that the angles of the tie-down lashings are at most something like 30°. But because we always have faith in our fellow man, we may be tempted to think of a light load, in which case these rather alarming angles could have been sufficient to lash down the load provided that all the necessary anti-slip mats had been used properly. Hard on the heels of this thought, we notice that the long steel rollers are solid, which would give a total weight of around 7 tonnes. And at this point, any illusions that the securing may just about have been adequate are dashed. So we have to change tack and have a cool, analytical look at the photos.
- Let us first concentrate on the aspect of friction. We can see plenty of anti-slip material in the photos, underneath the dunnage, the load itself and the wedges. But if we have a closer look at the photos, we see that large pieces of anti-slip material have only been placed under the ends of the square lumber that has been used as dunnage. But at the points where the 7-tonne load is "forcing" the lumber onto the loading surface, there is no anti-slip material to be seen. Under these circumstances, the good coefficient of friction μ of 0.6 usually provided by the anti-slip mats cannot be assumed.
- As we have already mentioned, the wooden dunnage has a square cross-section and also has rounded corners from the sides of the log. This cross-section is almost circular, and under load the dunnage will react accordingly. On square dunnage, the load will roll. It has become something of a mantra in this column: when wooden dunnage is used, it should have a rectangular cross-section! If rectangular lumber is not available, two pieces of square dunnage can be bolted together to make a rectangular format. And we stress the word "bolted", as a nailed joint is not able to withstand the expected loads. Depending on the diameter of the bolts, they must be fitted in cleanly drilled holes and appropriate washers must be used when joining the lumber. This is the only way of ensuring that the dunnage cannot roll. Ideally, such artificial rectangular dunnage or proper rectangular dunnage should have anti-slip material glued to or laid on both sides so that there is an unbroken friction train between the load and the loading surface. The excellent friction qualities of the anti-slip mats only work to best effect if this is the case. In the case we are looking at today, the level of friction that would apply under load is a matter of chance, but safety has nothing to do with chance.
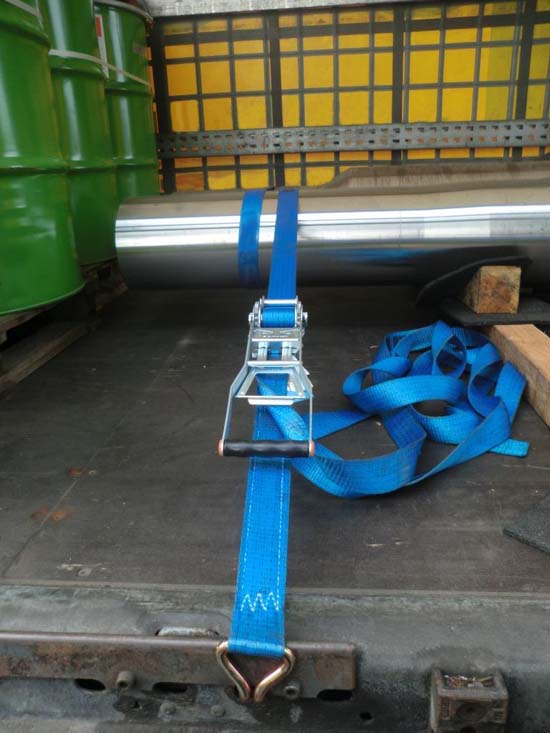
Figure 2 [Daniel Heyer]
The issues with this load are compounded by the fact that hazardous cargo has been stowed more or less directly in front of the load of steel. So, the fact that the 7 tonnes of steel rollers are inadequately secured is not the only problem we have with this load. Far from it. If the rollers slip forwards, it is pretty well guaranteed that they will destroy several steel drums containing flammable liquid, which would then run out. We do not need to paint the consequences of that scenario. But let's get back to the load securing: Figure 2 shows a magnificent blue belt with a long-lever ratchet handle. This belt has been attached as a round-turn lashing. This means that the belt has been passed completely round the steel rollers and then secured and tensioned like a tie-down lashing. These lashings are also known as "silly loops", which is what they are called in the new CTU Code of Practice.
So why is it not particularly smart to secure loads in this way? The intention of securing a load in this way is twofold: to bundle the load and to lash it down at the same time. Unfortunately, the load is only bundled by the friction of the belt on the extremely smooth steel surface. It is friction only that "secures" the load to the sides. A round-turn lashing like this at first appears to resemble a loop lashing (sometimes known as a half-loop lashing or a C lashing). But a loop lashing would need to come from the right-hand side, be taken around the load and secured again on the right-hand side. And the same would need to be done on the left. A loop lashing like this secures the load with the actual LC (lashing capacity) of the belt. Because we are talking about two ends of the same belt, the load will be secured with 4000 decanewtons (daN) in one direction if the belt has an LC of 2000 daN. Because such loop lashings need to be used both at the front and at the back, these two steel rollers would be secured with a securing force of 8000 daN both to the left and to the right. The extremely shallow angles only reduce the effectiveness of the securing arrangement by 1 or 2 percent, which is negligible. Admittedly, two loop lashings require twice as much material and twice as much effort as a single round-turn lashing. But the securing force to the sides is 20 to 30 times greater, so such lashings are far from silly!
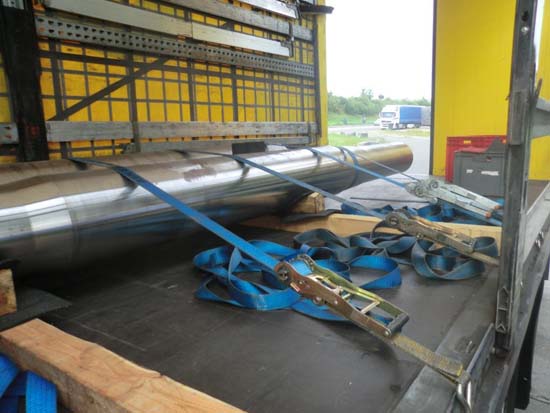
Figure 3 [Daniel Heyer]
In total, the steel rollers were secured by five tie-down lashings, with the front and rear tie-downs taking the form of round-turn lashings. Another drawback with round turn lashings results from the fact that the belt is passed once around the complete load. This causes so much friction that no pre-tensioning force whatsoever reaches the other side.
So what was the securing effect that was achieved?
With five tie-down lashings, all of which have been tensioned with long-lever ratchet handles, it is possible to achieve 5 x 750 daN (3750 daN) on the side on which the belts are tensioned and 3000 daN on the opposite side. This would give 6750 daN total pre-tensioning force. Which is a considerable amount! To be generous to whoever took such pains to secure the load sensibly, we shall assume that the belts are at an angle of 30°. This reduces the vertical component of the belts to 50 % or 3375 daN, and this vertical component now acts solely on the basis of friction. Here again, we shall assume a constant coefficient of friction μ of 0.6, which gives us an effective securing force of 2025 daN. This particular load would have needed just 1400 daN in the direction of travel.
Figure 3 clearly shows that unfortunately there is no anti-slip material under the squared lumber in the middle of the vehicle at the point at which the load is resting on the dunnage. The photo also shows that the dunnage has a square cross-section with significantly rounded corners. In this case, the high levels of friction cannot act at all, as the dunnage would simply roll under load, causing the load to slip forwards, with the only friction being a mixture of rolling friction and the friction between steel and wood.
What securing forces apply to the sides?
In the vast majority of cases, securing the load in the direction of travel is the most important thing, as longitudinal acceleration is by far the most significant factor. When dealing with cylindrical loads, however, particular attention must be paid to securing the load to the sides. In the case of this load, wedges were used, and the anti-slip material was placed both on and under the wedges, which is the right way to do it. So far so good! Unfortunately, the wedges were not nailed in place. These wedges were just lying unsecured on top of the anti-slip material. This means that it was a matter of chance whether the load would have pressed the wedges onto the anti-slip material in time as it rolled to the side, or whether the wedges would have been pressed out from between the anti-slip material by the rolling cylinders. Either way, as soon as the squared lumber tips over under longitudinal acceleration, the wedges would drop onto the loading bed and the load would only be restrained to the sides by the round-turn lashings. And, as we have explained, these lashings rely solely on friction, and the load would therefore move on the loading bed virtually unsecured to the sides. We have already described how loop lashings would offer a relatively simple and highly effective solution under Figure 2.
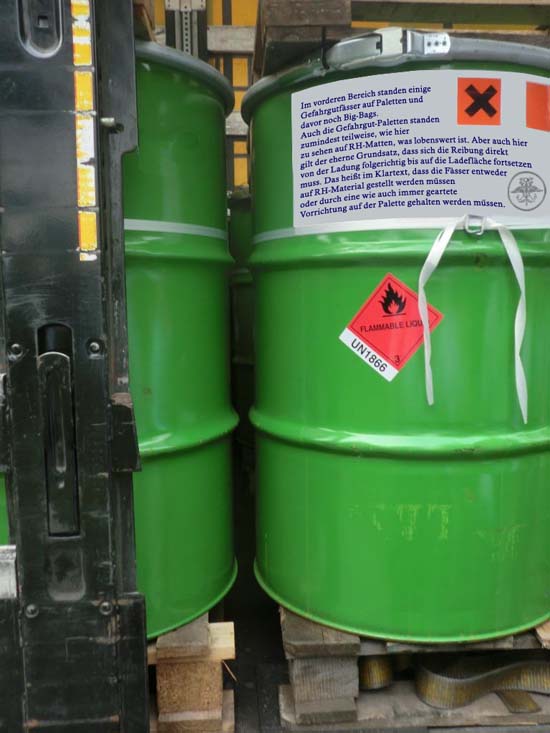
Figure 4 [Daniel Heyer]
A number of drums of hazardous cargo were stowed on pallets at the front of the vehicle, and big bags were placed in front of these. We shall return to these later. The photos show that at least some of the pallets with the hazardous cargo were standing on anti-slip mats, which is laudable. But once again, the immutable principle applies: Friction must be passed directly from the load to the loading surface without interruption. In other words, the drums must either be placed on anti-slip mats or they must be attached to the pallet by some kind of mechanism.
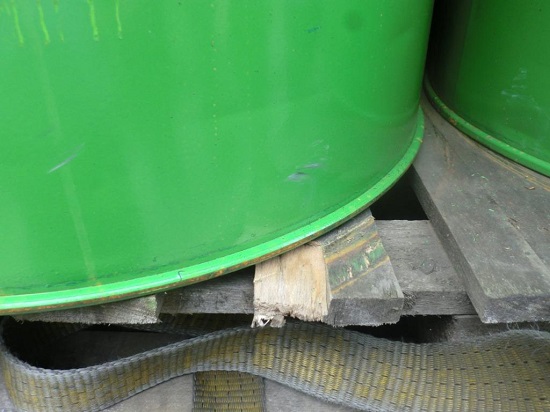
Figure 5 [Daniel Heyer]
We can clearly see that the load has already shifted significantly, and Figure 5 also clearly shows that the drums have already slipped forwards over the edge of the pallets.
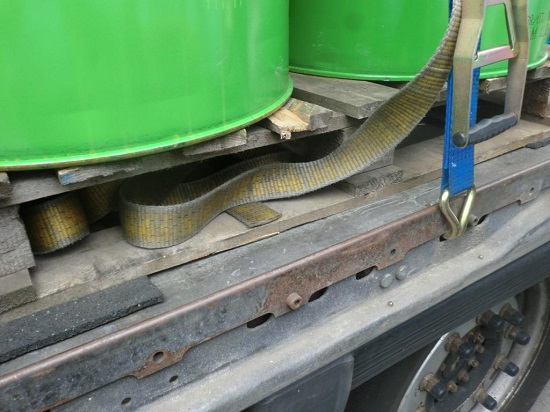
Figure 6 [Daniel Heyer]
This figure shows why all the efforts that were clearly made to properly secure the pallets with the drums of hazardous cargo ultimately failed. This pallet is bearing a weight of at least 800 kg. On the side on which the belt is tensioned, the ratchet handle of the lashing belt is also pressing against the pallet with a force of at least 500 daN. The friction-enhancing mats were only placed under the corners of the pallet and the center of the pallet is resting directly on the loading surface without any friction-enhancing materials. Although we would not necessarily wish to reduce the overall friction to a value of 0.3 or 0.4, we are simply unable to say how much of the total friction comes from the anti-slip mats and how much from the friction pair consisting of wood and loading surface. Any responsible police officer inspecting this load would in all probability ignore the anti-slip mats when assessing the friction, a decision which we fully appreciate. At the risk of infuriating our regular readers, we repeat: When anti-slip materials are placed under a load, this should be done in such a way that the load is completely isolated from the loading surface in terms of friction, i.e. it is lifted so that it is no longer in contact.
How can this be prevented effectively?
In the following diagram (1), we present an idea which can, of course, be further developed.
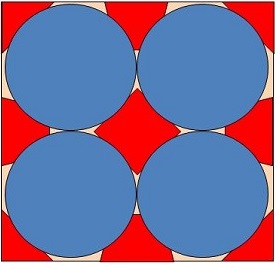
Diagram 1 [GDV]
The wooden panels secured to the pallet keep the narrow corrugated drums, which tend to tip, away from each other and, above all, keep them on the pallet. Lozenge-like wooden elements that can be secured to the center of the pallet are available on the market.
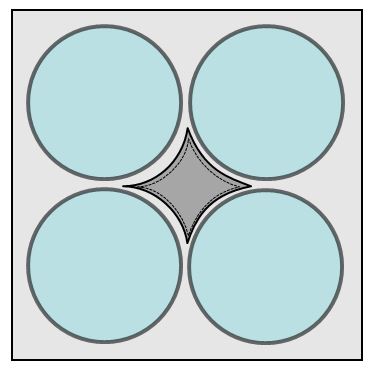
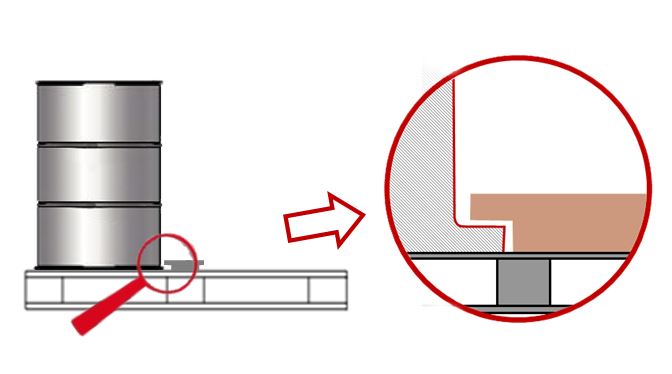
Diagram 2 [GDV]
With this solution, the way in which the lozenges are secured to the pallet is of particular significance.
These wooden lozenges feature a groove to accommodate the lower rim of the drum. Now, the four drums only need to be bundled together on the pallet with a plastic strap (as can be seen in Figure 4) both at the top and bottom. This prevents the drums from moving on the pallet. To prevent any movement at the top of the drums, similar lozenge-shaped spacers can be placed on top of the load. If these elements also feature guides for the belts (these can take any form), the drums can be secured efficiently and safely on any loading surface provided that anti-slip mats are used.
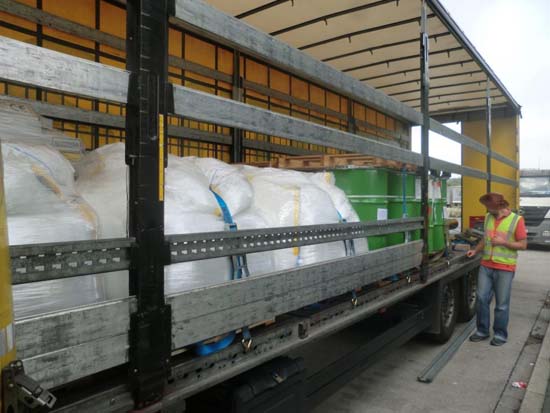
Figure 7 [Daniel Heyer]
This figure clearly shows that considerable attention was paid to securing the drums of hazardous cargo. A total of four pallets were placed on top of the drums to allow them to be lashed down at all. Figure 6 reveals exactly how successful this attempt was. "Big bags" were placed at the front of the vehicle, and these too were lashed down. Recently, the industry has devoted a considerable amount of energy to categorizing loads for transportation in big bags, in order to allow them to be secured in some way (unfortunately, usually with tie-down lashings). Unfortunately, we load-securing columnists have no complete market survey available to us, but we assume that at least 95 % of all granulate in big bags has characteristics that prevents it from being secured effectively with tie-down lashings. Of course, a tight fit represents a good way of securing such loads. In this case, an excellent tight fit has been achieved to the end wall at the front and to the drums at the rear. Unfortunately, there is no such tight fit to the sides. Nevertheless, and this deserves praise, an attempt was made to compensate for the lack of a tight fit to the sides with a tie-down lashing, despite the existence of a good tight fit to front and rear.
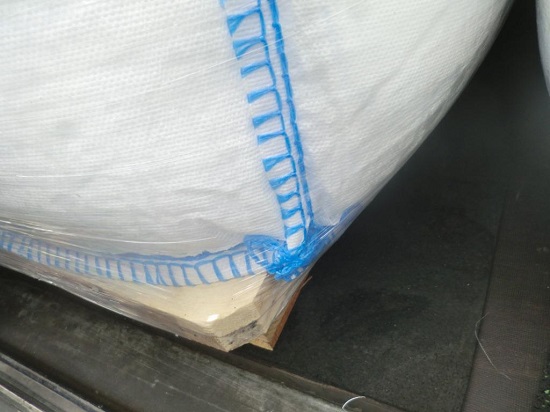
Figure 8 [Daniel Heyer]
In many cases, the problem with palletized loads (as with the drums) is the way that the load is attached to the pallet to form a load unit. The critical area is, of course, the bottom of the load, where it stands on the pallet. Because the load-securing columnists recently took part in a training course on shrink film, they know that the connection between the load and the pallet is the crucial area when forming a load unit. If the load is slightly smaller than the pallet, it is possible to join the load and the pallet perfectly well if the film is applied correctly. If, however, the load protrudes over the pallet, this is no longer possible. The fact that the load is larger than the pallet prevents them from being married properly.
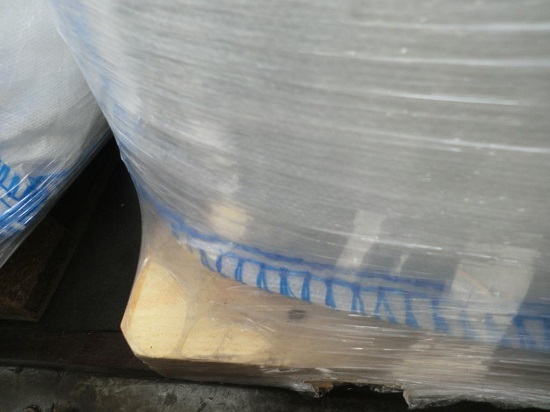
Figure 9 [Daniel Heyer]
Figure 9 shows that the film is badly torn at the corner of the pallet. This can hardly be said to constitute an effective connection.
Summary: How to improve the safety of the load
Let's start with the rollers at the rear:
- Use rectangular wooden dunnage
- Attach anti-slip material to both sides of the dunnage
- Nail wedges onto the dunnage to secure the load to the sides
- Use four tie-down lashings to maintain the good level of friction and to ensure that the load is adequately secured in the direction of travel
- Use two additional loop lashings on each side at the front and back to provide the best possible securing to the sides
Securing the steel drums:
- Place them as a tight fit to the front against the big bags
- Place anti-slip material under the pallets
- Place anti-slip material under the drums or use "lozenges" at the top and bottom
- As was done, place pallets on the top and use tie-down lashings to lash the load down
- Use a head loop lashing in the direction of travel if necessary
Securing the big bags
- Place them as a tight fit against the end wall
- Use pallets that correspond to the footprint of the big bags
- Use sufficiently strong film to wrap or shrink-wrap the bags to the pallets
- Lash down the big bags and again attach a head loop lashing in the direction of travel to support the end wall in its securing capacity.
When using any of the securing suggestions above, make sure that the loading surface is swept clean before the cargo is loaded.
This should ensure that there will be no problem transporting the load safely.
We wish you a safe and secure journey.
Your Load Securing Team
Back to beginning