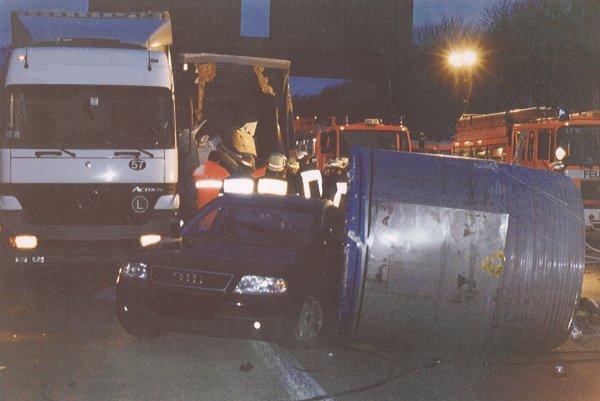
Figure 21a: The result of a 5 cm load gap, 23 t of steel and hard braking! [Cologne local authority, ABI Ost, VD]
Sequence of events leading to the accident:
An articulated truck (40 t maximum gross weight) is loaded with a steel coil (23 t in weight). The coil lies with the eye (winding axis) longitudinal to the direction of travel in a coil trough and is „secured“ by overlashing with a lashing belt (with an admissible lashing force Fadm of 4000 daN). Two stanchions are located in front of the coil, but, as was subsequently established, at a distance of 5 cm from it. At a speed of 70 km/h, the driver has to brake hard and swerve to the left.
The assessor established the following course of events:
The lashing belt tears. Because the coil is not directly supported (the gap is 5 cm), it begins to tip over, bends the stanchions over to an angle of approx. 45° and begins to turn. The coil rolls over the stanchion, which, having bent, acts as a ramp, through the headboard of the trailer, crushes the cab, falls onto the roadway and comes to rest on the boot of an Audi automobile standing in front of the truck. All but one of the applied steel straps (coil packaging) come loose during the accident. The remaining (circumferential) strap is only just able to prevent the sheet steel from completely unrolling. The truck driver survives, but is severely injured. (He was trapped in the wreckage of his cab for about 3 hours before he could be cut free by the fire service.) No-one was injured in the automobile.
Analysis:
The trailer had a coil trough and, providing that the correct span and angle of the trough were selected, the vehicle was suitable for transporting coils with the winding axis in the direction of travel. The vehicle also had two stanchions which, in direct contact with the load, may likewise be considered suitable for securing the load in the direction of travel. The overlashed 4000 daN belt secured the coil against „dynamic“ rolling. The question of coil stability in the direction of travel could not be resolved conclusively at the time of writing, as the precise dimensions could not be ascertained. To the extent that it is possible to determine the dimensions of the coil from the Figures, the coil was not stable – it needed to be additionally secured against tipping in the longitudinal direction of the vehicle (in accordance with VDI 2700 and 2702).
The loading gap allowed the coil to begin to tip. Once the coil had begun to tip, the tie-down lashing could not stop it. Had the coil been loaded in direct contact with the stanchions, it is very likely that the outcome of this accident would have been different. Because the driver swerved to the left at the same time as braking hard, the coil was able to rotate into a „rolling“ position. Virtually no energy was absorbed by the unobstructed rolling to the headboard and the coil was thus able to roll through the headboard and the cab.
According to the GDV Cargo Securing Manual, the load could only be made truly safe by placing it flush with the edge of the cradle and in direct contact with the stanchions and by two tie-downs and two lashings through the eye of the coil. In accordance with GDV recommendations, the two lashings through the eye should be taken to the rear to ensure that the load is additionally tightly secured in the direction of travel. The load should also be tightly secured to the rear (either by the inserted coil trough cover or by appropriately placed lashings).
Friction-enhancing materials should be firmly installed in the coil trough.