Box components | [German version] |
Boxes consist principally of bottom, side and end walls, lid and various inserts inside the box. Figure 1 shows the individual components.

Figure 1: Box components
1 – end wall | 4 – lower transverse batten | 7 – diagonal batten | 10 – longitudinal skid |
2 – side wall | 5 – upper longitudinal batten | 8 – end beam | 11 – rope lifting battens |
3 – upper transverse batten | 6 – lower longitudinal batten | 9 – bottom board |

Bottom
The bottom should be viewed as the most important component of a box, since it has to absorb both the forces applied from above (stack pressure) and those applied to the box from below (by forklift trucks, ropes etc.).
Appropriate pockets or lifting points have to be provided under a box in particular for handling of the boxes using forklift trucks and cranes. This is achieved by attaching transverse skids or rope lifting and sliding battens. In so doing, care must be taken to arrange the pick-up points symmetrically relative to the center of gravity of the box, to ensure safe transport.
As shown in the following Figure, the pockets should be arranged in such a way as to allow safe handling by forklift truck.
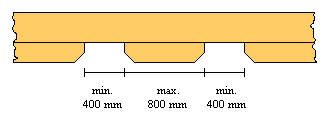
Figure 2: Position of pockets
To secure the package contents against slippage and tipping in the box, it must be screwed to the box bottom. The screws should extend through the skids (see Figure 3). Certain package contents (e.g. statues), which cannot be secured with screws, must be held in place by a tight fit (see Figure 4).
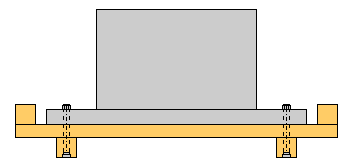
Figure 3: Securing with screws
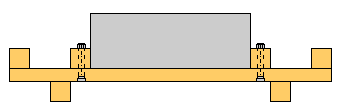
Figure 4: Tight fit
To give the box the necessary transverse strength, the longitudinal skids are screwed to end beams. Additional transverse bracing (transverse rope lifting battens etc.) may also be fitted to increase rigidity.
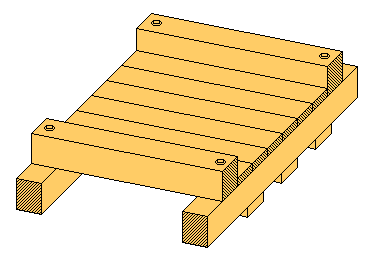
Figure 5: Box bottom with end beams
In the case of package contents with a relatively narrow standing area, the load should be distributed to all the skids by crosspieces to avoid point loads. If the standing area of the package contents is smaller in dimension than the upper area of the package contents, load distribution can likewise be improved by bracing.
Back to beginning

Side and end walls
Side and end walls come under strain from stack pressure forces during storage and from dynamic forces during handling. The boarding forming the side and end walls should be vertical, since it absorbs vertical forces better than does horizontal boarding. To increase the strength of the box structure and to conduct the compressive forces arising as a result of stacking into the bottom of the box, the end and side walls are fitted with transverse, longitudinal, vertical and diagonal battens. Each side or end wall requires one upper and one lower longitudinal or transverse batten respectively. One vertical batten should be attached to the end wall per longitudinal skid. The number of vertical battens attached to the side wall depends on the length of the box, but the distance between them should not exceed 1000 mm. Alternatively, vertical posts may be fitted instead of vertical battens. Diagonal battens must be fitted if the internal height of the box is greater than 1500 mm. The individual battens should be arranged as in Figure 1.
Back to beginning

Lid
The box lid, which either lies directly on the end and side walls or on an appropriate frame structure, generally consists of a single layer of boards and a framework of battens. It has to absorb both the stack pressure forces which arise when several boxes or the like are stored on top of one another, and transverse compressive forces. These arise during cargo handling as a result of the use of ropes or chains. To prevent damage to the lid boards as a result of transverse compressive forces, they should be fitted as illustrated in Figures 6 and 7.
![]() |
Figure 6: The lid board is set back somewhat. |
![]() |
Figure 7: The lid board is positioned against the side boarding. |
![]() |
Figure 8: On hoisting, the rope may lift the lid board and loosen or detach the boarding. |
Back to beginning

Inserts
Inserts serve mainly to fix the package contents in the box (bracing etc.) and to transmit the forces acting on the lid to the box bottom. In smaller boxes this may be achieved directly via the longitudinal, transverse and vertical battens. Boxes with a large lid area have additionally to be provided with lid girders.
If the lid girders are attached directly to the upper longitudinal and transverse battens, point loads arise which would result in the battens caving in under high stack pressures.
To avoid point loading of the battens, vertical posts may be built into the inside of the box for the lid to lie on. This structure has a very high loading capacity, but has the considerable disadvantage that the boxes have to be larger to accommodate the vertical posts.
A third option for securing the lid girders is to use CP connectors (named for the company Cargo Pack), which help to prevent point-loading of the longitudinal and transverse battens. For assembly purposes, the CP connector is driven into the lid girder and fixed to the side wall with two nails. CP connectors have the advantage over vertical posts of not requiring any additional space while still exhibiting almost as high a loading capacity.
Figures 9 to 12 show the various ways of securing lid girders (in darker color).
![]() |
Figure 9: The lid girder is mounted directly on the longitudinal batten where it gives rise to point loading |
![]() |
Figure 10: The lid girder is attached by means of a vertical post and ends at the longitudinal batten, the forces thus being uniformly distributed. It is clear that the space inside the box is reduced considerably by the posts. |
![]() |
Figure 11: The lid girder is secured with a CP connector (in red). The lid rests uniformly on the bracing and the internal volume of the box is not reduced. |
![]() |
Figure 12: The CP connector is driven into the longitudinal batten and secured with two nails, here lying one behind the other. The lid lies flat on the girder. |
Back to beginning