Photo of the Month – May 2024 |
[German version] |
Almost everything right!
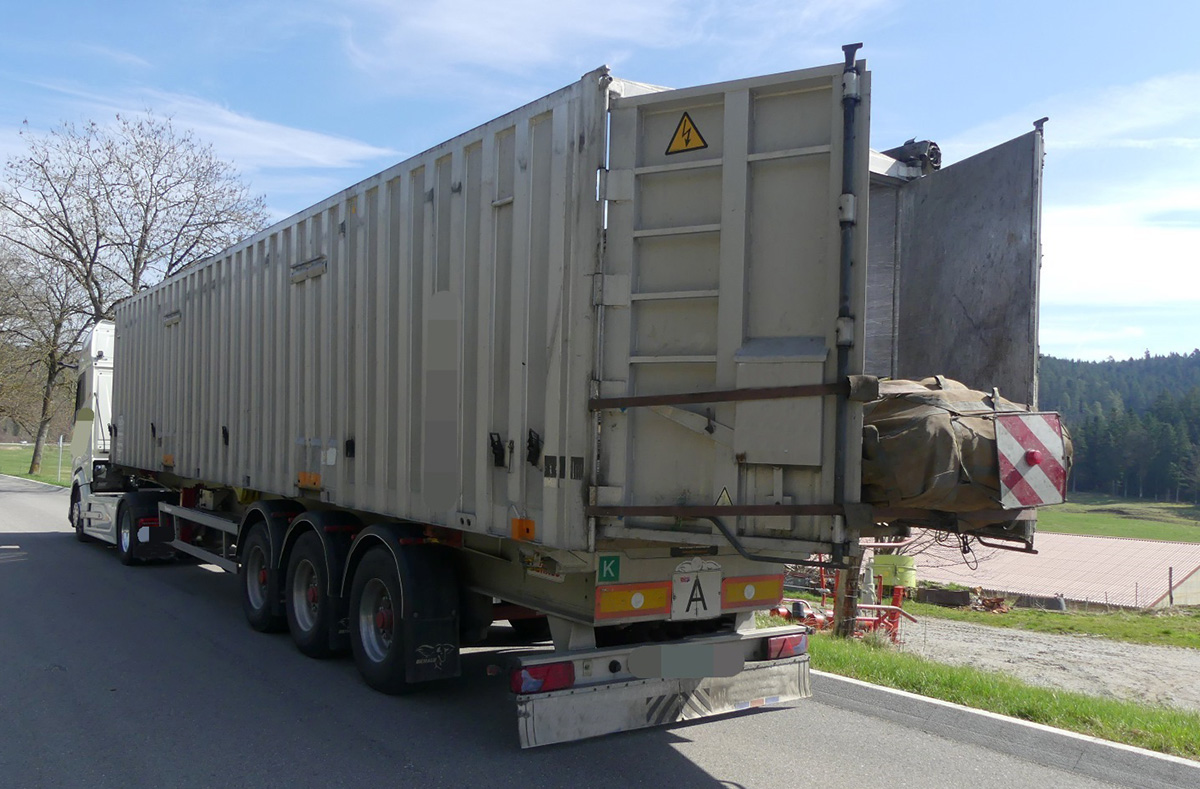
Figure 1 [Max Reich]
A trailer laden with 29.5 tonnes of bundled steel of the type commonly referred to as structural steel. We also do not know of any specific industrial term. The vehicle, or more precisely the trailer, is very interesting. It is constructed rather like a container, open at the top, can be covered with a tarpaulin and is clearly suitable for combined (intermodal) transport. We can see that it is intended for this form of transport by the grappler pockets (see the yellow marking directly above the middle axle of the rear axle assembly). We could not find the corresponding elongated approval plate in the photos. However, this did not form part of this inspection. The fact that the trailer is approved for intermodal transport tells us that its load-bearing capacity is probably comparable to that of a Code XL trailer. For the purposes of our calculations, we shall assume that the rear wall has a load-bearing capacity of 13,500 daN (although this would, of course, have to be verified on a case-by-case basis). The opened out “A”-plate actually indicates that waste was being transported. However, this plate does not have to be closed up if a normal load is being transported.
The load protrudes beyond the back of the vehicle and belts have therefore been used to secure the doors in an open position. This means that the length of the vehicle has been extended and that a special permit is therefore required. However, that, too, is not the subject of today’s article. As always, we are interested in the load securing.
The total weight of the vehicle together with its load was just about 44 tonnes. Although that is, generally speaking, permitted for precarriage and onward carriage in intermodal transport operations, such weights are nevertheless subject to certain conditions. On the one hand, intermodal transportation must be at least theoretically possible and the idea of transporting trailers with excess-length cargo in this way appears difficult to us to (maritime transport on a ferry would undoubtedly be possible). For this vehicle combination to be authorized to carry 44 tonnes, the axle distances must be greater or the weight must be distributed over six axles; otherwise, this combination may only carry 42 tonnes.
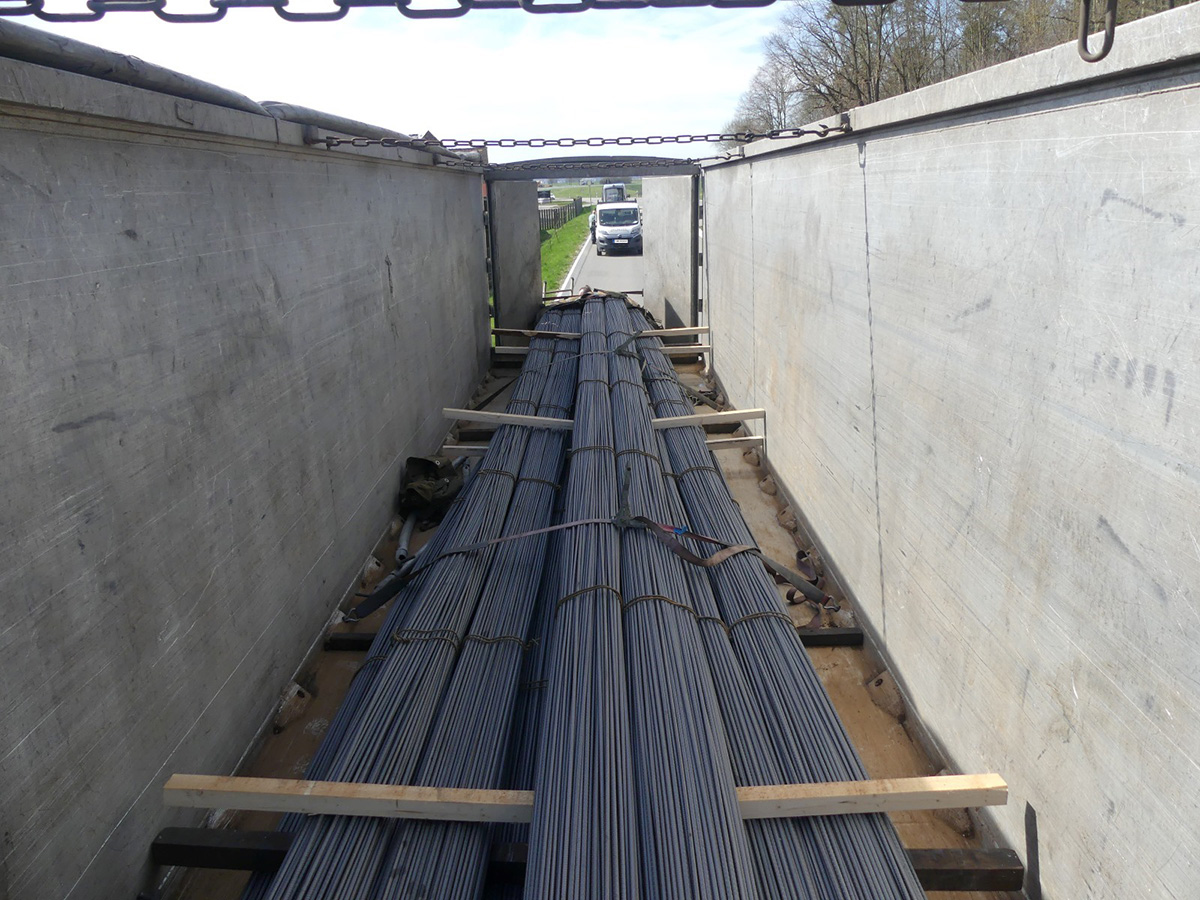
Figure 2 [Max Reich]
The load is lying on base and intermediate wooden dunnage, which we estimate to have a coefficient of friction (µ) of 0.3. It is secured by means of three tie-down lashings with a pre-tensioning force of 750 daN. For the purposes of this general overview, we shall not consider the angles. 2,250 daN x 0.3 results in a securing force of 675 daN.
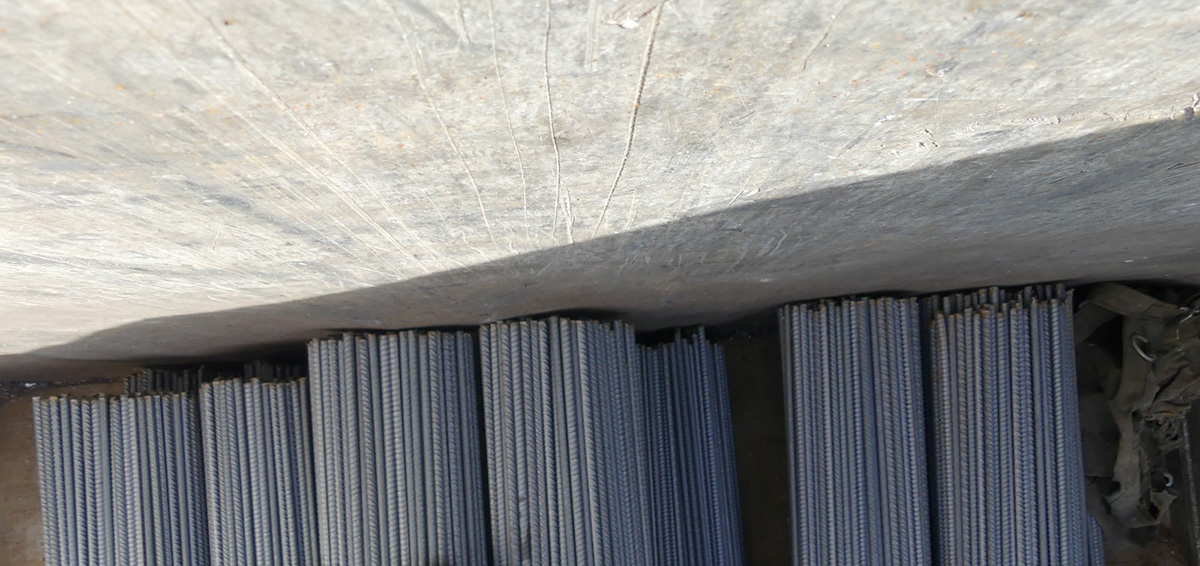
Figure 3 [Max Reich]
A bird’s eye view of the load at the end wall.
The load is lying at the end wall as a tight fit (or very nearly). Because the load protrudes at the back, it was decided not to perform any load distribution at the end wall. However, we consider this to be essential because the end wall can only provide its 13,500 daN of securing force if the load is distributed across the entire width. At least four pieces of squared lumber are needed here to distribute the load against the end wall across the entire width of the vehicle. For the purposes of our calculations, we shall assume a correct tight fit. The load weighs 29.5 tonnes and we assume friction of µ = 0.3. We therefore need 14,750 daN of securing force. The end wall provides 13,500 daN and the tie-down lashings 675 daN. We are therefore missing 575 daN of securing force.
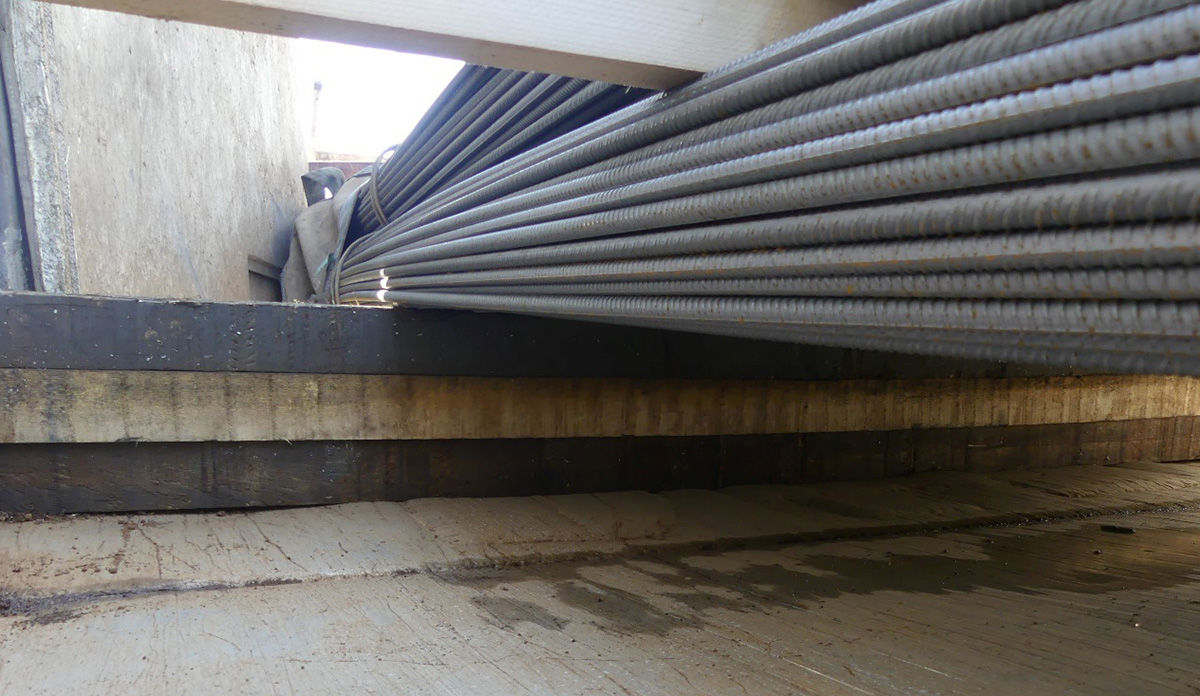
Figure 4 [Max Reich]
When we consider the load securing to the rear, we are struck by two things:
1.) The load at the rear was raised so that it was able to develop some measure of static pressure toward the front and…
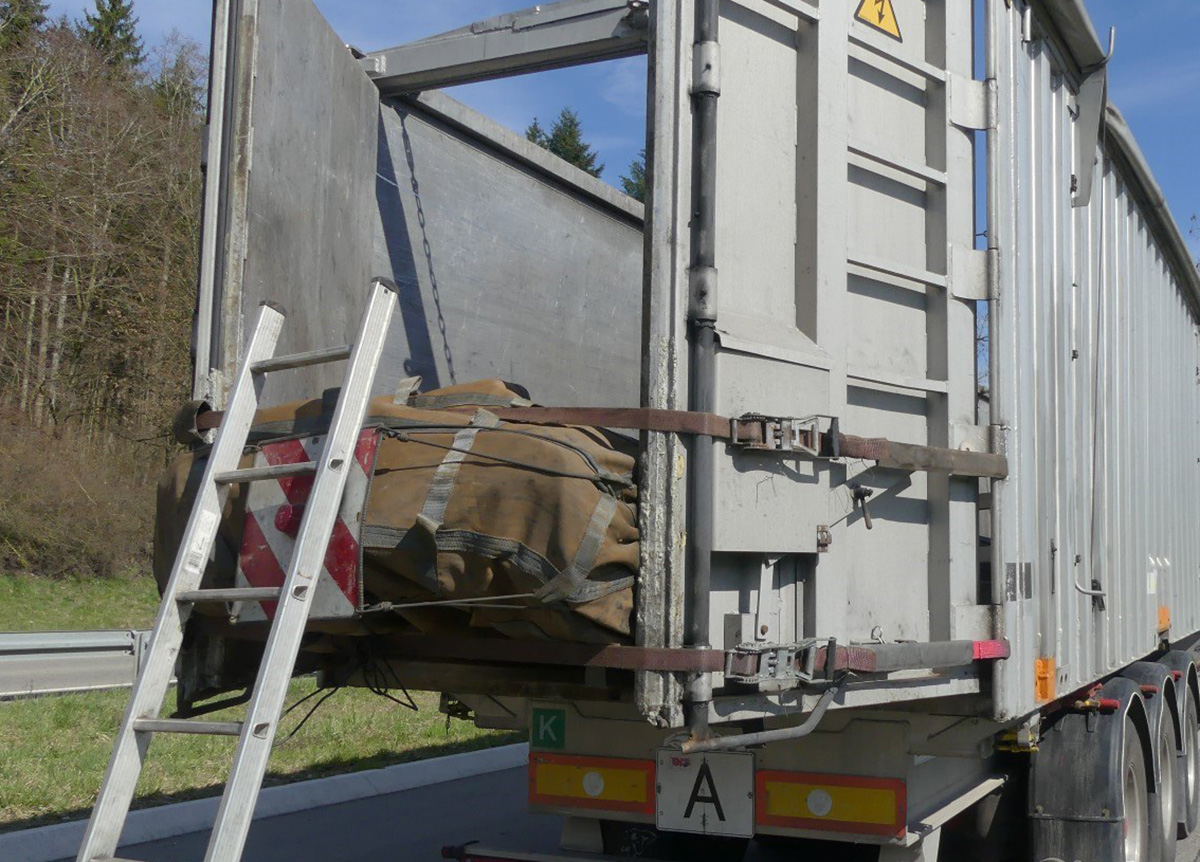
Figure 5 [Max Reich]
2.) A “load securing bag” was placed over the load – which is an excellent idea. These bags give loads of this type a certain tight fit to the rear, but only if the load securing points present on the bag are bound to lashing points on the vehicle by means of direct lashings. This was unfortunately not the case here.
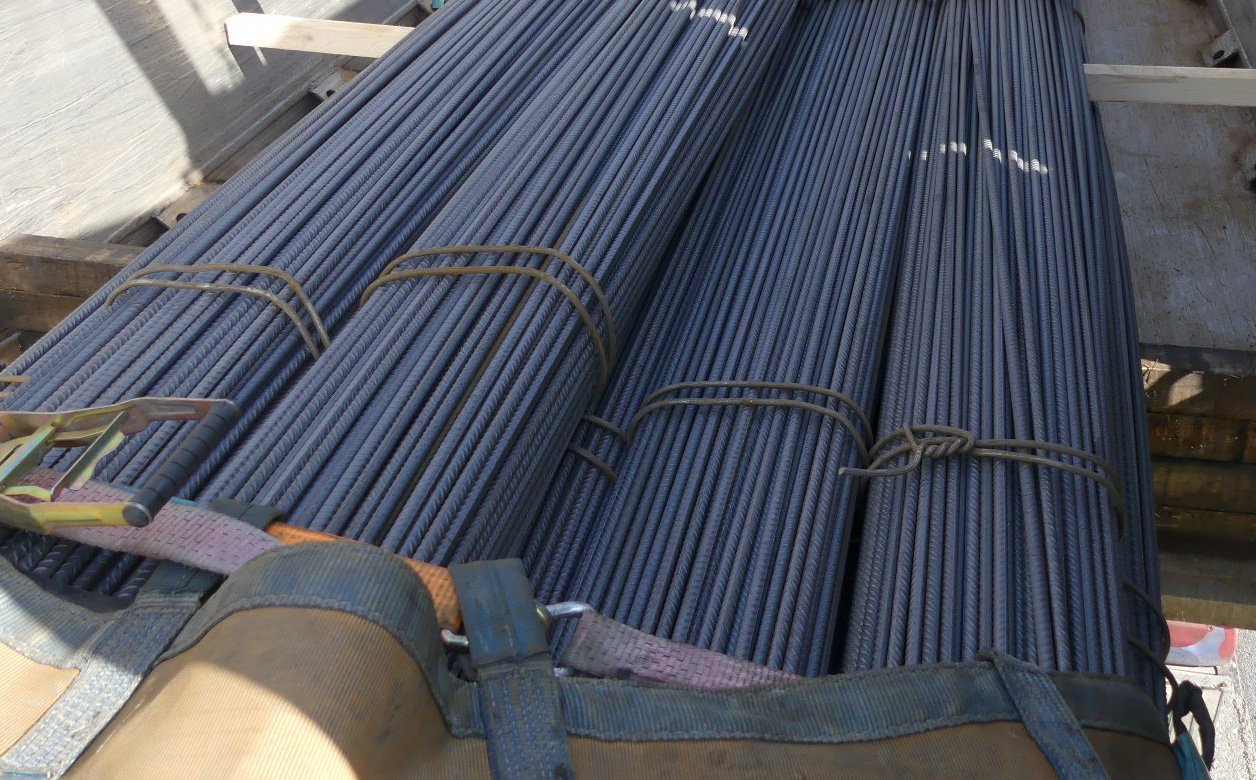
Figure 6 [Max Reich]
Although the load was neatly bundled with a belt, none of the load securing points have been used. The raised position of the load is of no use if a strain is applied because the free-standing stack will tip over and the wonderful load securing bag is also of no help because the three direct lashings that are needed are missing. We would attach four direct lashings to ensure that the load securing bag is evenly secured.
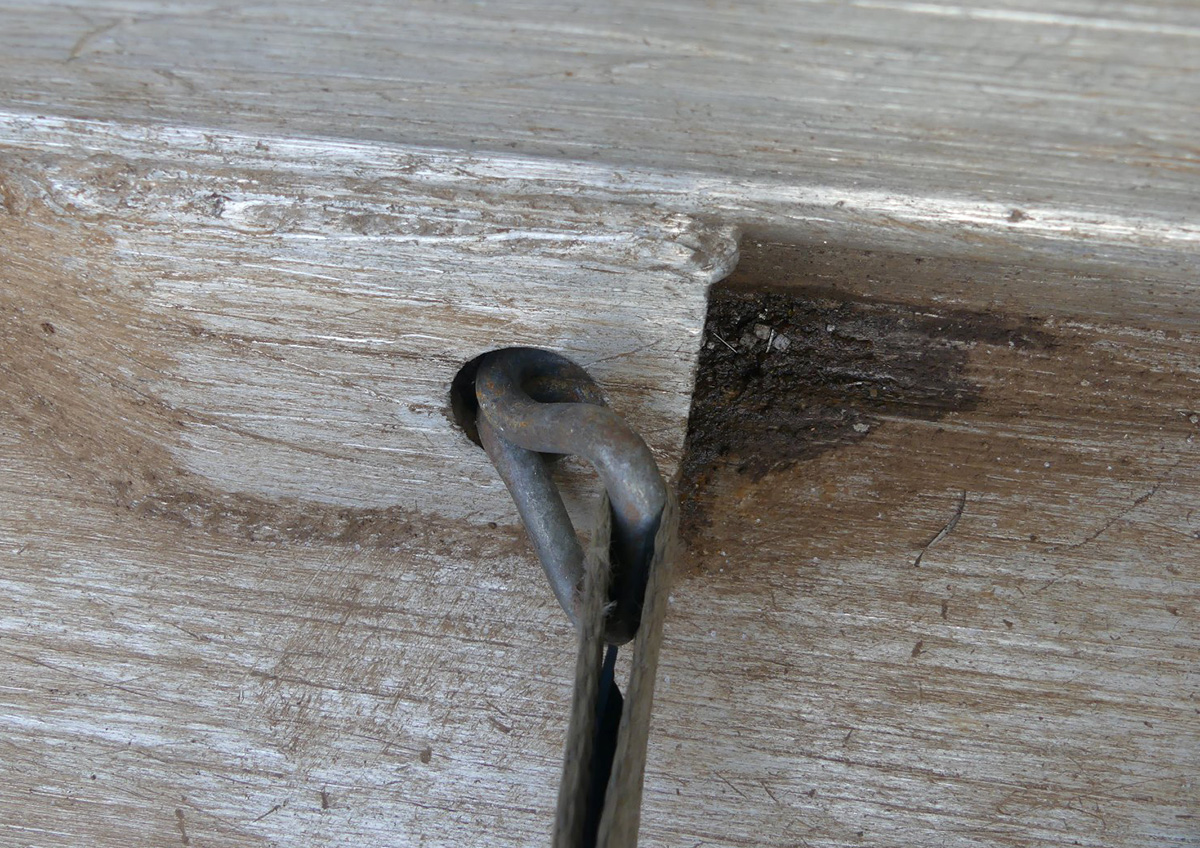
Figure 7 [Max Reich]
The load securing points in this container were carefully chosen and shaped in such a way that it was very difficult for bulk material to get caught in them. Unfortunately, the hooks of the load securing equipment were not suitable for the load securing points because they were all attached in a way that made them liable to bend open (as can be seen in this photo). What was actually needed were larger hooks since then the load would have been applied at the shoulder. Shackles or adapters could also clearly have been of help here. However, the direct lashing for the “load securing bag” would have worked and the hooks would have been loaded at the shoulder.
Securing of the load:
There is almost no load securing to the side. We would use loop lashings to perform this task. As the load is stowed, the bottom two layers and the top two layers must each be secured with four loop lashings. To do this, we would use belts or chains, which we would lay out on the loading surface before starting to load the trailer so that we could then guide them back over the load after loading and secure them to the relevant side. If belts are used then it is advisable to protect these with protective sleeves. Although chains might not be quite so easy to handle, they are also not as sensitive and do not need any separate protection. Because each loop lashing also has a component that acts as a tie-down lashing, we now have eight “tie-down lashings”. As the structural steel was loaded together as a tight fit, it is easy to apply the pre-tensioning and hold the load securely to the sides using the direct lashings. The tie-down lashing components of the loop lashings increase the friction to such an extent that the missing securing forces to the front are easily made good.
We have already discussed the load securing to the rear and so all that is left is to wish you a safe journey at all times!
Your Load Securing Team
Back to beginning