Photo of the month – October 2023 |
[German version] |
Friction, Friction, Friction
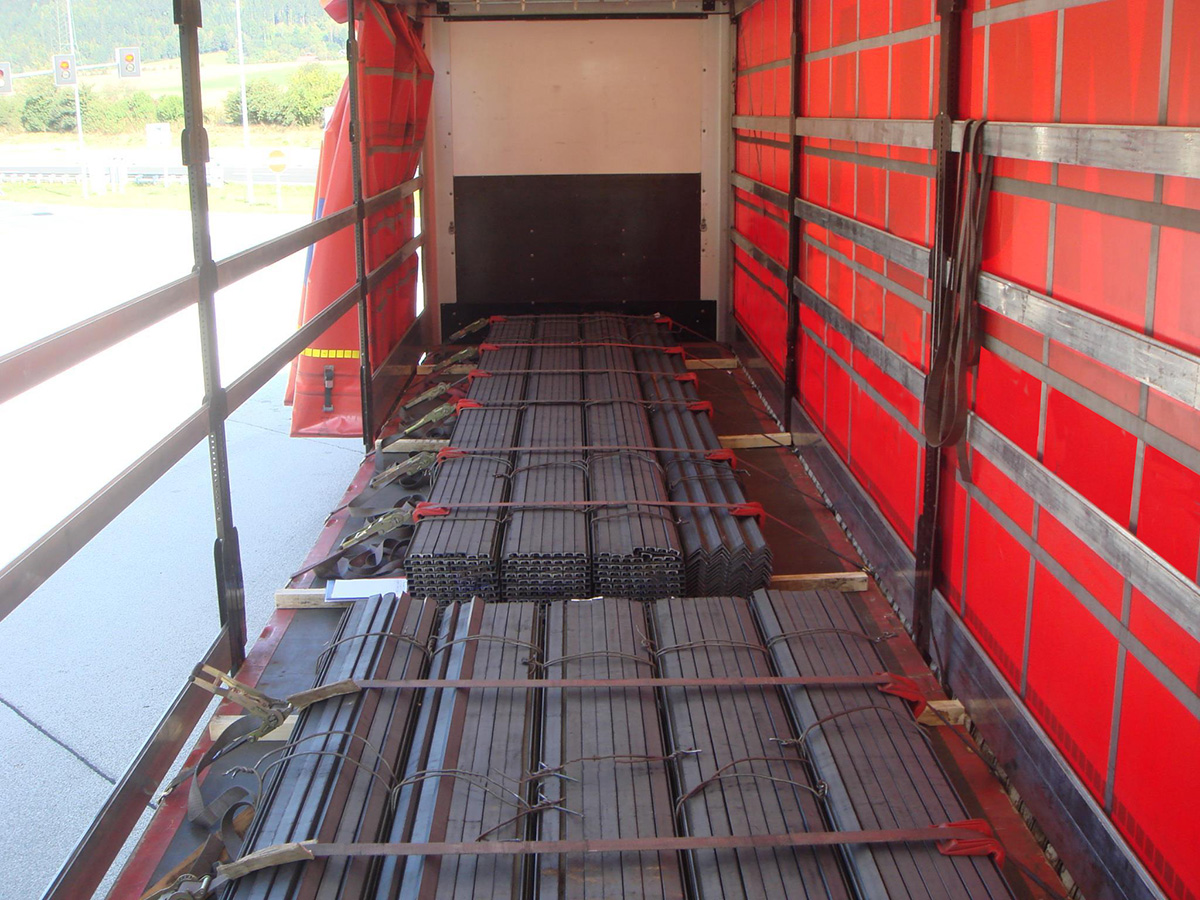
Figure 1 [Karl-Heinz Pachoinig]
In Figure 1, we can see a full load of U-profiles together with a bundle of angle sections. Due to reasons of load distribution, less of the load is at the front than at the back. In each part of the load, we can see six belts used as tie-down lashings with edge protectors and it is also clear that the individual packages are only very loosely bundled.
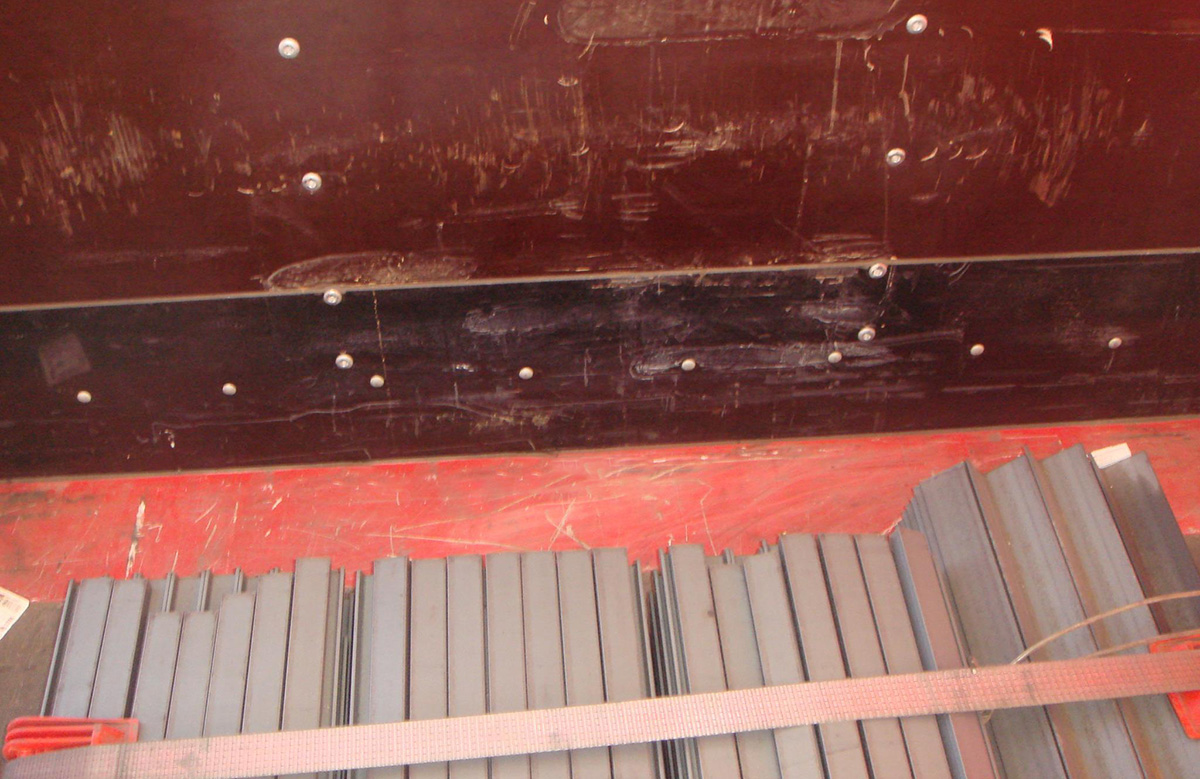
Figure 2 [Karl-Heinz Pachoinig]
Figure 2 reveals that there is no tight fit to the end wall, which has already undergone a repair, and Figure 3 shows that there is also no tight fit between the individual packages making up the load.
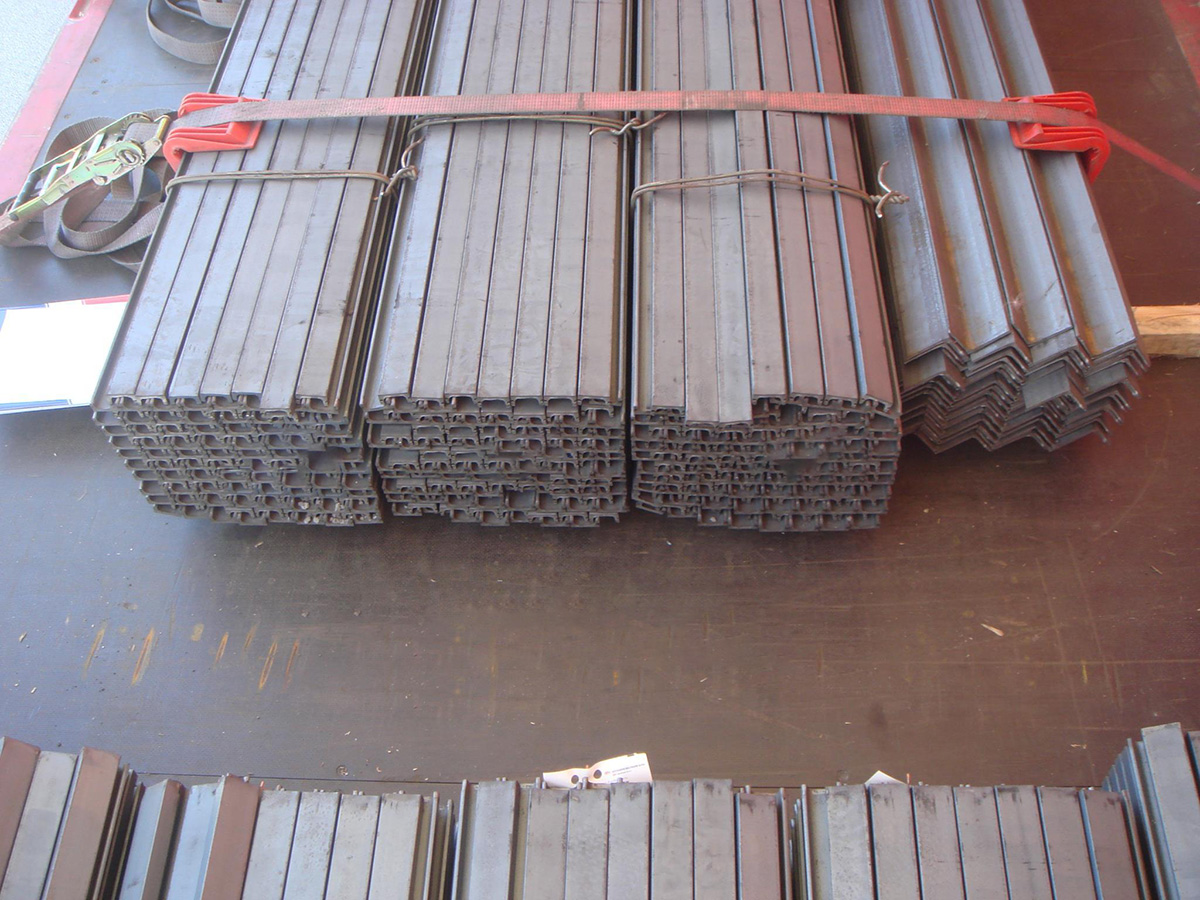
Figure 3 [Karl-Heinz Pachoinig]
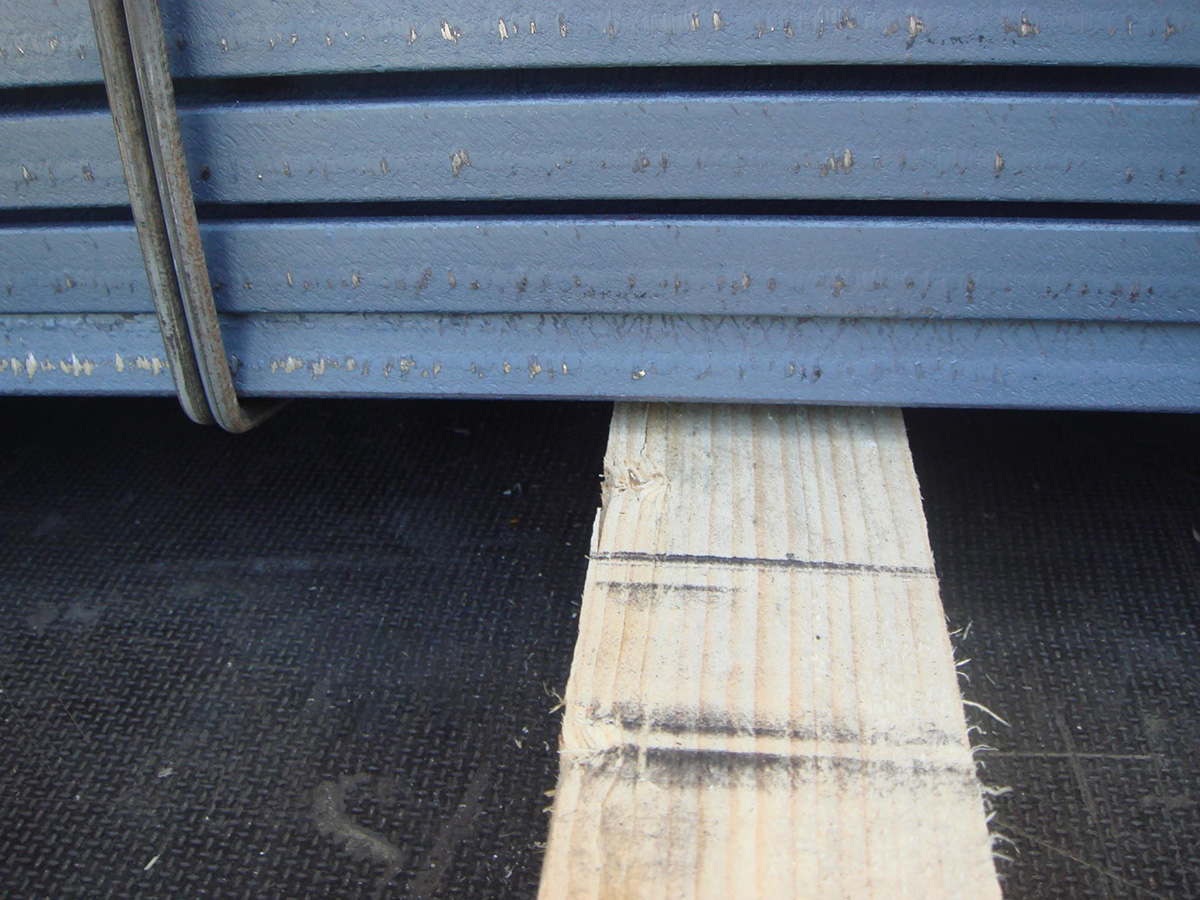
Figure 4 [Karl-Heinz Pachoinig]
The load is lying on squared lumber which is, unfortunately, literally square. But that is not what we want to talk about here since we want to concentrate on friction. The U-profiles appear to have a sort of mill scale on them. They might have a coefficient of friction of μ = 0.3 but in the absence of any measurements, we prefer to assume a value of μ = 0.2 to be on the safe side. The friction against the wood undoubtedly has a coefficient of μ = 0.4, but this is true only of the bottommost layer. Apart from that, we have steel on steel and the loose way the packages are bundled means that they do not form effective load units.
Securing the load:
The load-securing measures taken consisted of 12 tie-down lashings for 24 tonnes of steel with a coefficient of friction of µ = 0.2. The angle was not as much as 40&grad;, meaning that probably only 60% of the pre-tensioning force acted vertically. Even though not all the ratchets had long levers, we assume a pre-tensioning force of 1,000 daN per belt because edge protectors were used throughout. This results in 12,000 daN of pre-tensioning force, which we shall multiply by 0.60 (sine at an angle of 37 degrees). This leaves us with 7,200 daN of vertically-acting pre-tensioning force. However, since the pre-tensioning force only acts via the friction, we now have to multiply this by the coefficient of friction μ = 0.2. The remaining securing force therefore amounts to 1440 daN. The value needed for this load is actually 14,400 daN. The shortfall in securing force is therefore enormous and would have been even if we had assumed μ = 0.3.
What we suggest to improve load securing:
Regular readers of our column will already have started muttering the words direct lashing and loop lashing to themselves… and rightly so given that steel that is only bundled into secondary packages and therefore does not form a load unit in itself cannot be viably secured using anti-slip material. Here, the load-securing measures have to do two things at once:
- They have to secure the load
- And they have to bundle it so that the various items can be handled together.
If load-distribution considerations mean that it is possible to load the front packages directly at the end wall then, to improve load distribution, we would stack several pieces of squared lumber on top of one another there and load the cargo as a tight-fit against them. We would choose lumber of a length that covers approximately 90% of the width of the vehicle in order to ensure optimum pressure distribution.
Because using the end wall greatly simplifies our task, the load should be distributed in a way that meets the demands of the load distribution curve. If that is not possible given the load distribution presented in our example then another option would be to position the angle sections at the rear part of the load.
If the load is positioned up against the end wall then none of the sections can escape forwards. However, we still need to secure the load to the side and to the rear. We use two loop lashings on each side to secure the load laterally. If the belts are distributed across separate load-securing points then these loop lashings will hold well over 3,000 daN (depending on the angle). Since we have to use two loop lashings on either side, we have secured the load to the side with more than 6,000 daN. The belts are thoroughly pre-tensioned and therefore effectively bundle the load.
Warning: It is important to use edge protection sleeves because almost every bit of this steel is abrasive.
Load securing to the rear can be achieved using two upright pallets that are secured using a loop lashing.
The second part of the load, which in our example weighs 16 tonnes, must also be secured using a tight fit. To do this, we stack squared lumber resting on two pieces of wood arranged in the direction of travel in front of the front face of the load. Given a weight force of 16,000 daN and a coefficient of friction of μ = 0.2, we need 9,600 daN of securing force. This corresponds to three loop lashings which we arrange to be all the same length. Here again, it is important to use edge protection sleeves because we are still dealing with abrasive edges.
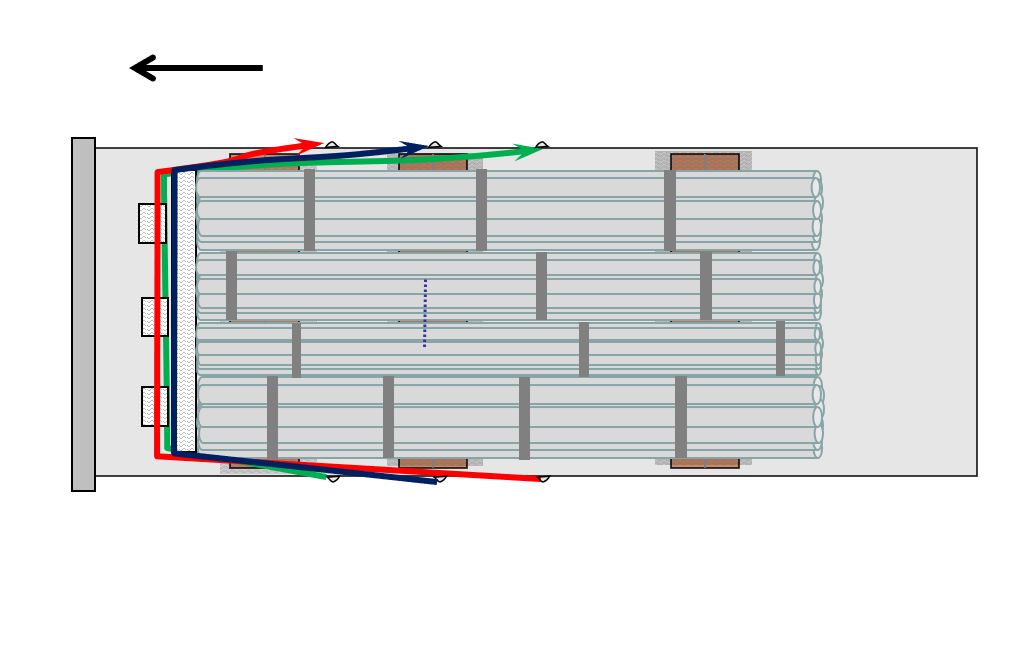
Diagram 1 [Photo of the Month]
The securing measures to the side and rear are the same as for the front package.
Your load securing columnists wish you a bright and colorful autumn.
Back to beginning