Photo of the month – January 2022 |
[German version] |
Lord of the rings
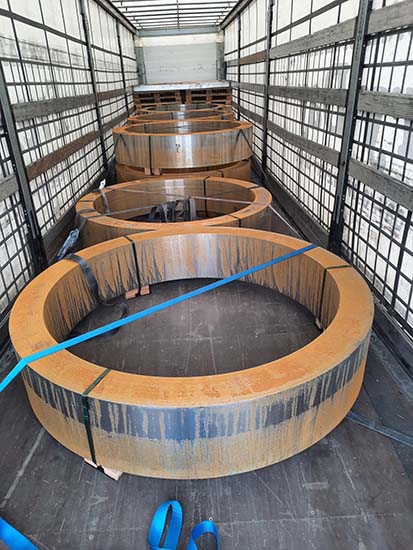
Figure 1 [Raymond Lausberg]
This particular lord of the rings comes from Southeastern Europe and has been living in his truck for 15 weeks without ever going back to his home country, let alone back to his home. We have very little doubt that he has never taken part in or seen a load-securing course. Even the distribution of the load is entirely wrong. And this despite the fact that there are two rows of pallets at the end wall (one crosswise and one lengthwise), thus moving the first load unit 2 m further back. The first three load units are made up of stacked rings, with the two rear ones being loaded in a single layer. Each ring weighs a good 3 tonnes, which puts far too much weight on the drive axle. If the rings had been loaded the other way round, i.e. stacked at the rear and loaded in a single layer at the front, the load distribution curve would undoubtedly have been perfectly acceptable.
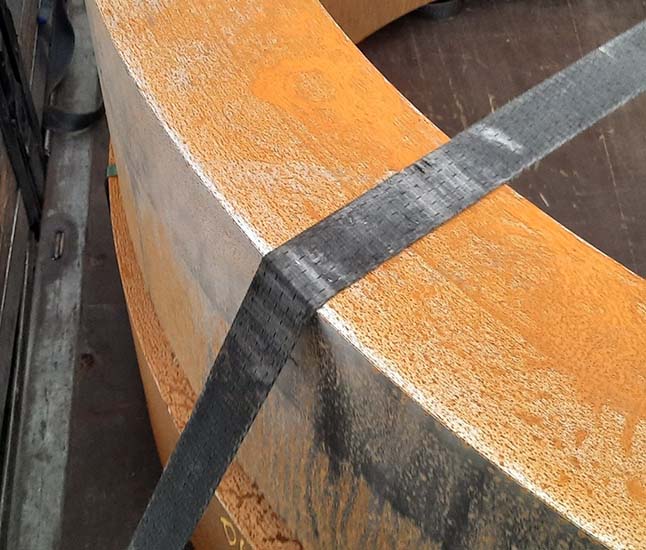
Figure 2 [Raymond Lausberg]
This photo shows one of the key flaws in the attempt to load and secure this cargo. Sharp edges and no edge protectors. And the whole thing is “secured” with a belt that has pretty well reached the end of its life, as it is not only showing signs of wear but already has cut marks.
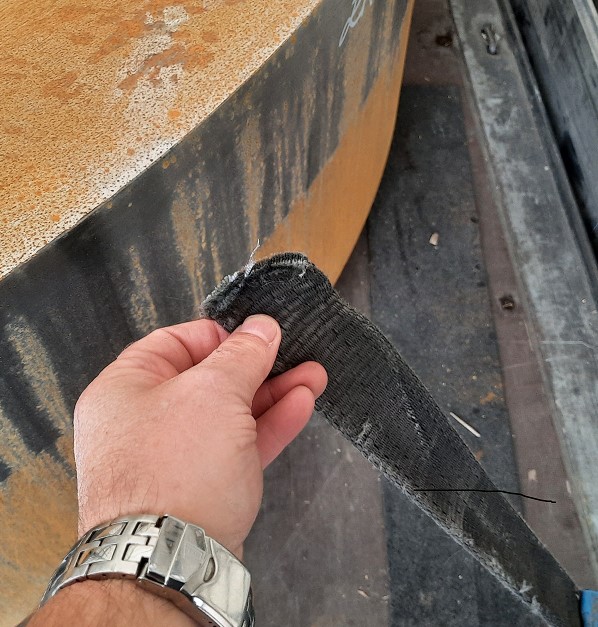
Figure 3 [Raymond Lausberg]
And this belt is in a rather worse condition. The sharp edges have already done their worst on the first few kilometers (10 to be precise) of the trip. Cut clean through and the load being secured with a tie-down lashing was a thing of the past.
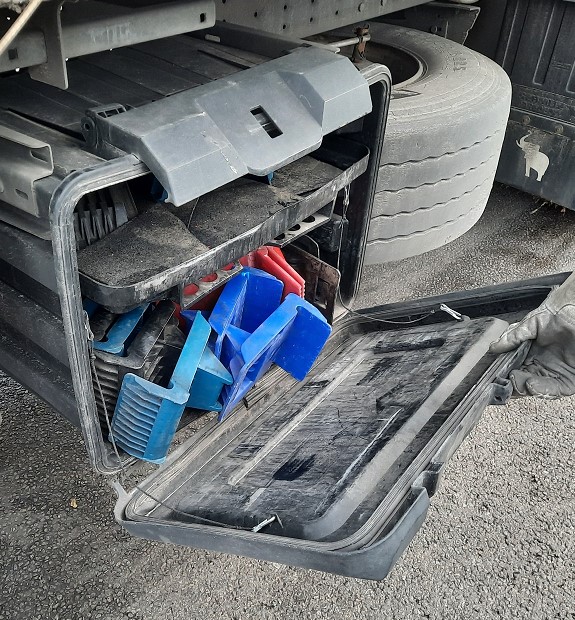
Figure 4 [Raymond Lausberg]
We really have no idea why the driver did not use the plentiful edge protectors that were available. Perhaps because they have a tendency to break when used with round or cylindrical loads. If this is the case, the vehicle was not carrying the proper equipment, and this once again lies in the responsibility of the carrier – a point we shall return to later.
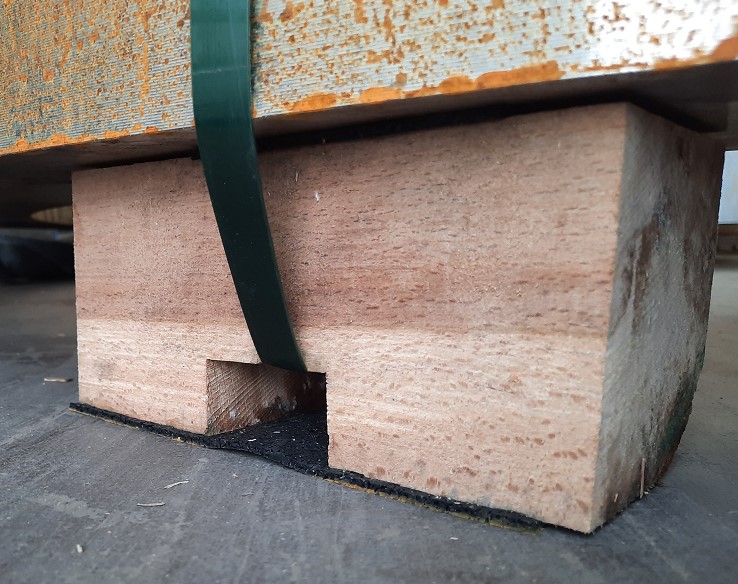
Figure 5 [Raymond Lausberg]
We shall look at the friction to establish whether the use of tie-down lashings was in principle a good idea. The rings were each standing on three wooden blocks that were attached with plastic straps. There was anti-slip material underneath the wooden blocks, as can be seen clearly in this photo. And there was also anti-slip material on top of the wooden blocks, although it did not cover the entire surface. The crucial issue is whether the load was isolated from the surface it was standing on in terms of friction. This photo suggests that this was the case, but we have no information on whether the same applied to all the rings and blocks. The quality of the anti-slip mats used is a further important factor. At the front, the bottom three blocks have to bear a load of six tonnes on a total surface area barely larger than three postcards. In such a case, we would urgently advise the use of heavy-duty mats. Indeed, the use of such mats is absolutely necessary. As far as the friction is concerned, we assume that sufficient anti-slip material has been use and will take a value for μ of 0.6.
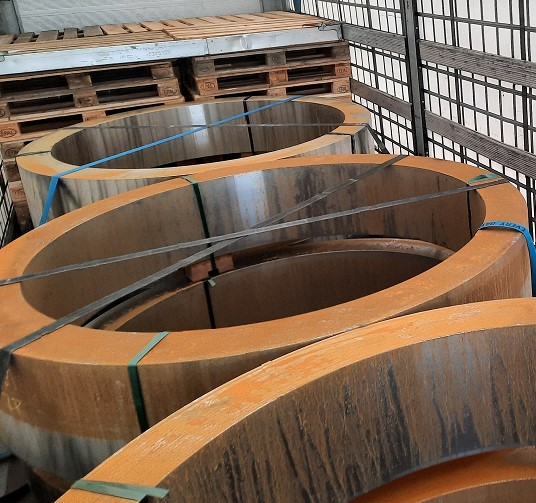
Figure 6 [Raymond Lausberg]
Given a coefficient of friction μ of 0.6, it is possible, at least theoretically, to secure even steel using tie-down lashings. For a weight force of 6000 daN, the residual securing force needed is 1200 daN. The angles achieved here mean that we can disregard them and assume a pre-tensioning force of 250 daN. We can double this to account for both sides and then double the pre-tensioning force again because we are using two belts, giving a total pre-tensioning force of 1000 daN. Friction supplies 600 daN of securing force. This means that 50 % of the required securing force has been achieved. The only problem is that all the securing measures on this vehicle may as well not exist because the belts were not protected from the sharp edges.
How to secure the load:
How would we have secured this load?
The arrangement with the blocks and with the very sparing use of anti-slip mats underneath seems somewhat flimsy to us. How will these stacks behave under load when the only thing to stop them from shifting is a single tie-down lashing? The same number of belts are capable of providing many times the securing effect of a tie-down lashing.
In the case of the stacked rings, four tie-down lashings would have been needed. If these four tie-down lashings had instead been used as direct lashings, twice the securing effect would have been achieved.
- Tight fit to the stacked pallets at the front
- The first two load units separate and not stacked, the rest stacked to distribute the load.
- Anti-slip material as shown, but somewhat more generous and systematically placed under and between the elements of the load.
- Edge protection sleeves used systematically, but we would not use angled edge protectors for this load, as we would need three for each individual loop lashing.
- One loop lashing at 90° to each side
- One loop lashing to the rear per load unit at as acute an angle as possible.
- The pre-tensioning force of the direct lashing provides the necessary minimum securing force
- The direct lashings to the rear are arranged at a shallow angle and provide two times 8000daN of securing force minus the angle. The formula cos alpha ½ applies for the loop lashing. We shall assume 30° and still achieve 97 % for the belt to the rear arranged at a shallow angle. Accounting for the angle along the longitudinal axis of the vehicle, we lose a maximum of 20 % in the direction of travel, which gives a loss of 23 %, leaving 6160 daN of securing force. Even if it were only half that, the load would still be perfectly secured with plenty to spare and no additional effort.
- If the load were arranged as a tight fit lengthwise, the following method could even be used:
- The first ring is secured as described above.
- The second ring would be secured with only two loop lashings to the sides.
- The third pair of rings is secured as above and the two pairs of rings loaded behind it are secured using only loop lashings to the sides.
- The load is adequately secured to the rear by friction and the minimum securing force.
Responsibility:
- The driver is always responsible.
- The carrier or freight forwarder must ensure that the vehicle is suitable and this includes the correct load securing material.
- The loader. The loader has the greatest influence and can contractually delegate load securing to the carrier / forwarder, but cannot delegate his responsibility. He must check that the contractual stipulations have been adhered to and preferably document this with pictures. In the case of cargoes such as this, it may make sense for the load to be secured by trained employees. This gives certainty and probably saves time.
If it is indeed the case that the edge protectors tend to break with the cylindrical load, the vehicle would not have been suitable, as it was not properly equipped. Edge protection sleeves would certainly be the method of choice for this load.
The loader obviously did not carry out a final check of the way in which the load was secured, otherwise the glaring deficiency would have been identified immediately. And the small number of tie-down lashings could not have been sufficient under any circumstances. This, too, would immediately catch the eye of a trained employee.
Your load securing columnists wish you a happy, healthy and safe 2022, a year in which we all hope to see the pandemic start to recede.
Back to beginning