Photo of the month – December 2013 |
[German version] |
Fatal friction
We constantly use this column to underscore the importance of friction. Friction and mechanisms to increase friction generally save those responsible for securing loads a great deal of effort. This also explains the widespread use of anti-slip mats. This Photo of the Month gives a tragic example of the real importance of friction.
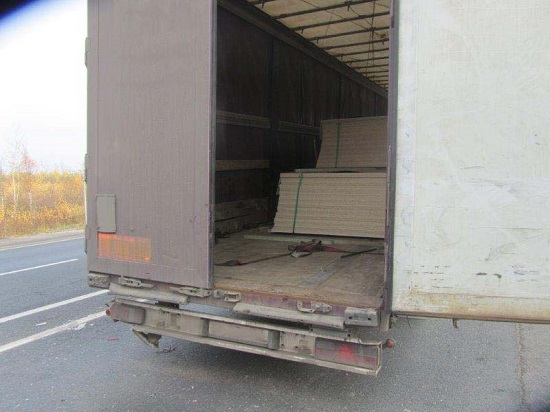
Figure 1 [Alexander Yanichek, St. Petersburg]
This vehicle was traveling along the motorway between St. Petersburg and Moscow. But the motorway could have been anywhere in Europe. The vehicle was carrying a full load of sheets of particleboard. Such a load brings with it several problems.
- It is extremely heavy.
- It has sharp edges.
- It has an extremely low coefficient of friction.
- Particleboard is a relatively low-value product, and so attempts are often made to minimize the costs involved in packaging and load securing.
Looking at Figure 1, we can only guess that the load has slipped forwards.
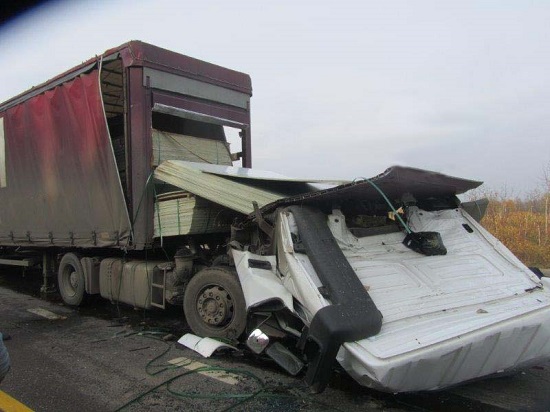
Figure 2 [Alexander Yanichek, St. Petersburg]
Figure 2 confirms that our guess was distressingly accurate. You can clearly see that unfortunately (as far as friction is concerned) the particle board here is coated, which means that its coefficient of friction is almost certainly even lower than the usual value for particleboard. It is estimated that the coefficient of friction for this coated particleboard lies below 0.1, perhaps 0.05 or even lower.
So how did this accident happen?
The driver had to brake to slow down on the motorway. The lack of friction meant that his load was unable to slow down, and it broke through the end wall of the trailer into the driver's cab, completely destroying it and pushing it forwards.
The driver did not survive the accident.
Unfortunately, we are unaware of how the load was secured. It is probable that tie-down lashings were used, as they are the simplest way of securing a load. And what is the principle behind this type of securing?
Pressure is applied to the load by pre-tensioning the belts. This pressure, or pre-tensioning force, applies an additional force that presses the load against the loading surface.
This increases friction. But it only makes sense to use this method if the weight of the load is not too great and the existing level of friction is already relatively high. After all, what friction is there to increase if the load has virtually no friction in the first place? If there is nothing there, it cannot be increased.
Packaging
The packaging was made up of plastic straps running crosswise and lengthwise. This packaging is primarily there to allow the load, i.e. the particleboard sheets, to be handled as a single load unit when moving it around the production plant and loading it. These plastic straps, which bundle the load to form a sensible load unit, are not to be confused with load securing measures. Sensible, effective bundling is of assistance when securing the load and poor bundling makes it harder to secure a load. If these packages are then stacked on the truck, these plastic straps not only have to keep their own package together, but also the one or two packages stacked on top of it. As a rule, they are unable to do this, because their job is to bundle the particleboard sheets to form a load unit.
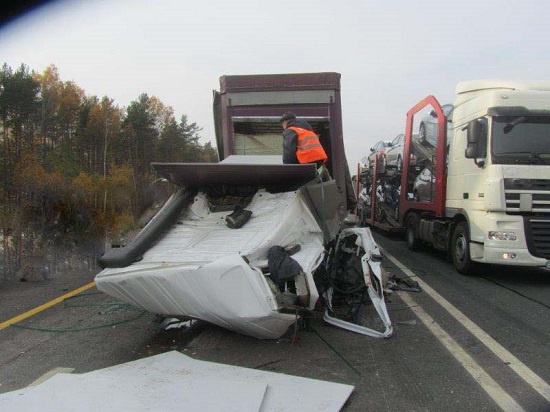
Figure 3 [Alexander Yanichek, St. Petersburg]
If the load has virtually no friction, it is up to the load securing equipment to deliver all of the necessary securing force. One way of doing this is to use stanchions that can be inserted in the center and at the sides of the loading area, and belts can be used for additional support. If stanchions are used to secure the load longitudinally by loading the packages as a tight fit against them, they must be strong enough to withstand the entire load placed behind them. Belts can also be used to provide additional support, but because the stretching properties of the woven synthetic textile belts are very different from those of the steel stanchions, the stanchions will first be subjected to most of the force, and only if these fail will the belts take up their full lashing capacity (LC). It is also possible to use chains to support the stanchions, but this runs into the problem that the particleboard is prone to damage.
Securing using belts
If loads like this are to be secured with belts, this can only be done using loop lashings and round-turn lashings. Such loop lashings have to be placed carefully in all potential directions of movement (to the front, to the rear, and to both sides). Because particleboard generally has extremely sharp edges, edge protectors must be used to protect the belts wherever they pass over the edges.
To recap: Before a belt is able to deliver its full lashing capacity, the load has to slip a couple of centimeters into the belt. Even this small amount of slippage is enough to allow a sharp edge to cut through a belt, but only if it is not adequately protected.
Responsibility
When we talk about responsibility, we can, of course, only refer to the situation under German law. In Germany, there are three layers of responsibility:
- The driver is always responsible.
- In parallel and with overlapping responsibilities, the loader is responsible.
- And, of course, the carrier is also responsible.
![]() | The carrier is responsible for ensuring that the vehicle is suitably equipped, that the vehicle itself is in good condition and that the driver is in a position to employ the provided load securing material appropriately. In addition, the vehicle used must always be capable of safely accommodating the load to be transported. |
![]() | Loader/driver: It is difficult to separate the responsibilities of these two parties, because both are responsible for load securing. One is responsible for ensuring that a load is secured in a way that it is safe to be on the roads and the other for securing a load in a way that it can be handled safely. In the case of this load, these responsibilities are largely identical. If the driver wishes to leave the loading point (e.g. the facility at which the particle board is produced) with an unsecured or inadequately secured load, the loader must prevent him from doing so. It would make sense if the loader were to clearly indicate the necessary load securing measures (for instance using pictograms on placards) and to instruct the loading personnel to check whether the securing methods recommended by the loader or similar methods have been used. The driver is, of course, free to choose a different securing method, provided that it is effective. If this accident, in which the driver lost his life, had happened in Germany, a German court would probably first check whether the vehicle was equipped with suitable load securing material and whether the driver was in a position to secure the load adequately. For instance, they would check whether the driver had attended training courses in load securing and been adequately instructed, and so on. There is no doubt that the driver did not fulfill his obligation to secure the load and has already paid for this mistake with his life. As a result, a German court would turn their attention to the next party involved, who also bears responsibility for load securing, and this is still the loader. In this column, we do not wish to speculate on the conclusions the court may reach, but it is patently obvious that any such investigation would be extremely uncomfortable for those responsible. |
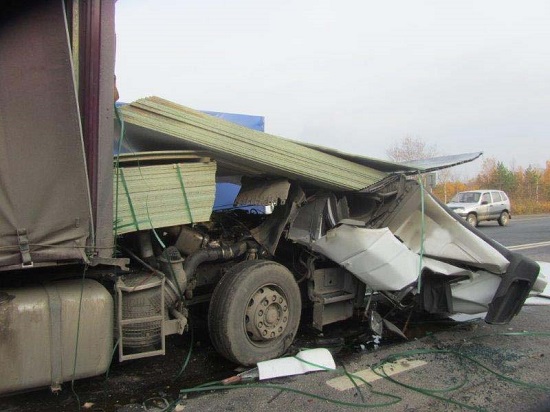
Figure 4 [Alexander Yanichek, St. Petersburg]
We often adopt a somewhat sarcastic tone in our column. With this Photo of the Month, we are saddened, struck by the enormity of what happened and filled with sympathy for the family of the driver who died. We hope that this case will help to massively increase awareness of the issue of load securing and heighten people's understanding of friction so that this death of one of our colleagues on the motorway was not in vain.
As we approach Christmas, our thoughts are with the family of the driver. May we wish you all a happy Christmas and a safe and successful new year.
Your Load Securing Team
Back to beginning