Photo of the month − December 2007 − Special 1 Version 1.0.0.08 |
[German version] |
A Christmas thought
The laws of physics do not take a Christmas vacation!
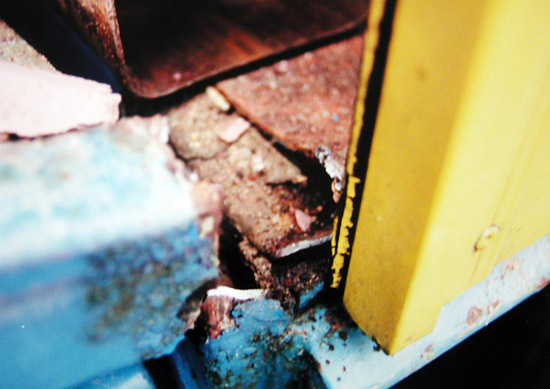
Figure 1 [R. Kessler-Kangler]
This was the inescapable conclusion when a headboard was faced with a challenge beyond its capabilities. Filigree slab concrete was loaded on a trailer. It rested on square steel pipes and was secured with one or more tie-down lashings. Since this was the only load unit on the trailer, it should have been placed significantly further back on the trailer in the interests of distributing the load sensibly. It is no longer possible to determine the extent to which this may have been the case. The loading area appears to be steel, as are the square pipes used to support the load. Figure 3 reveals two wide strips of friction-enhancing mats behind the load. On this basis, we can assume that the load had indeed been placed further back and was originally on friction-enhancing mats.
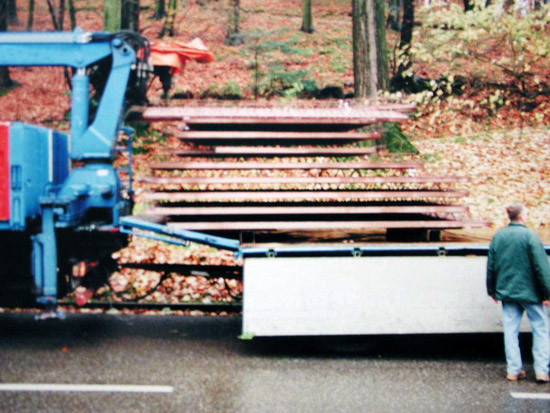
Figure 2 [R. Kessler-Kangler]
So what happened?
The use of one or two belts at most meant that the load was far from adequately secured. The attempt to use friction-enhancing mats to improve securing of the load is in itself laudable, but such measures must then be used consistently between all layers of the load. We shall not be discussing whether this would have been sensible for this type of load. One fundamental mistake was to use square steel pipes to support the load (the same applies to square lumber. Supports with a square cross-section facilitate rolling of the load along the longitudinal axis.
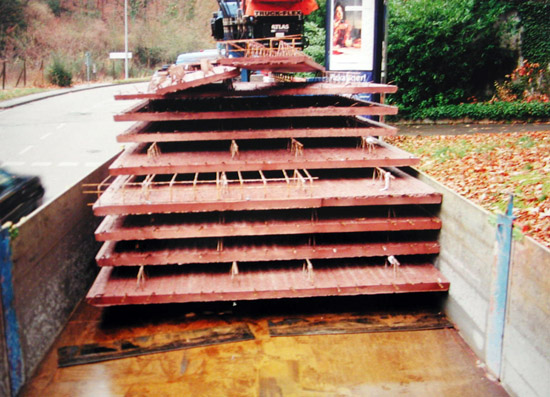
Figure 3 [R. Kessler-Kangler]
And then, on the way, it happened.
How is it possible to load and reliably secure a load of this type?
- Supporting materials with a rectangular cross section are to be used.
- If friction-enhancing materials are to be used (which certainly makes sense when steel is to rest on steel), it is necessary to make a "sandwich" by placing friction-enhancing materials between the loading surface and the support and between the support and the load. The coefficient of friction µ between filigree concrete slabs is given as 0.4 or higher in the literature, and this must be verified.
- If tie-down lashings are used, the required number needs to be calculated and actually used.
- The loose parts of the load to be seen on top of the load should not be incorporated in the tie-down lashing, as they can have a significant negative impact on the final securing and can reduce the time that the pre-tensioning is retained. In this case, loop lashings could have produced a reliable result.
- It would have been far better to use a vehicle fitted with load-securing points, since any load-securing mechanism that runs over the side walls drastically reduces the effectiveness of the securing and pre-tensioning and can even make it impossible to secure the load. Lashings of this type must be laboriously threaded under the side walls, which is good for neither the driver, nor the vehicle, nor the belts.
- Protection of the load-securing materials is of prime importance. As you can see on Figure 4, the lashing belt was sliced through cleanly when the load slipped. Elsewhere along its length, the belt is seriously damaged from the sharp edges of filigree concrete slab that had been transported previously. This damage alone is enough to consign these belts to the trash.
- Vehicles that provide the facility of inserting stanchions longitudinally or laterally offer a good method of securing the filigree concrete slabs as a tight-fit load. The load can be secured well to the side using loop lashings. If such loop lashings are prepared before loading, (i.e. if they are laid out on the loading area), the effort involved in securing the load once it has been loaded is relatively low and the result is highly effective.
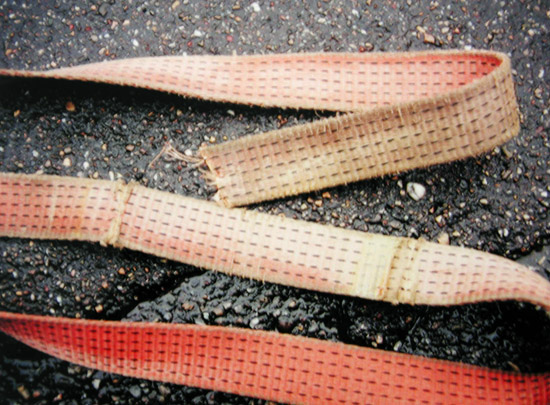
Figure 4 [R. Kessler-Kangler]
Back to beginning