Lade- und
Löschüberwachung in Südostasien – Schiffseignungsprüfung
|
Vortrag von Herrn Kap. Jochen
Hackstein, Gerling Konzern
Zusammengefasst von Herrn Kap. Uwe-Peter
Schieder, GDV |
Bei der Verladung von warm- oder kaltgewalzten Stahl gilt es grundsätzlich drei Hauptschadenarten zu vermeiden:
- Schäden durch Korrosion
- Händlingsschäden und
- Schäden durch mangelnde Ladungssicherung
Eine der Hauptschadenursachen ist das Eindringen von Seewasser in den Laderaum. Bei schlechtem Wetter gelangt Spritzwasser oder sogar wie es im Fachjargon bezeichnet wird „grünes Wasser“ (Brecher von Seewasser,
welche viele 10, ja sogar mehrere hundert Tonnen Wasser an Deck bringen) an Deck und kann dort durch unzureichend abgedichtete Lukendeckel in den Laderaum gelangen.
Da die Eignung eines Schiffes nicht allein von seiner Art und von seinem Alter abhängt, ist es überaus sinnvoll vor der Verladung eine
Schiffeignungsprüfung durchzuführen. Hierunter fallen die Inaugenscheinnahme des
Schiffes selbst unter Berücksichtigung des Erhaltungszustandes, Funktion der Lüftungsanlagen, Korrosionsgrad in den Luken, an Deck und insbesondere an den Lukendeckeln, Dichtigkeit von Ballastwassertanks etc. Bevorzugt sind Schiffe mit rechteckformatigen Laderäumen einzusetzen. Schrägen, wie insbesondere in Luke 1, aber auch in den Seiten eines Bulkcarriers bereiten bei der Verladung von Stückgut generell, aber auch insbesondere bei
Stahlladungen Probleme.
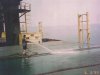
Abbildung 1 |
|
Sofern die generelle
Tauglichkeit des Schiffes festgestellt ist, ist es unablässig, eine
Dichtigkeitsprüfung der einzelnen Lukenabdeckungen bzw. deren
Dichtungen durchzuführen. Hierzu gibt es zwei Verfahren:
- Abspritzen der Lukendichtungen mittels Wassers und
- Prüfen der Dichtigkeit mittels Ultraschallgeräten (Sender &
Empfänger)
|
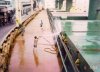
Abbildung 2 |
|
Das Abspritzen der
Lukendeckel mittels Wasser ist ein sehr aufwendiges Verfahren. Es
erfordert viel Zeit (je nach Lukengröße ein bis zwei Stunden pro
Luke) und Personal. Zusätzlich muss der Sachverständige ständig vor
Ort sein um das Abspritzen zu überwachen und um Leckagen zu
entdecken. |
Die Ultraschallmethode ist eine, durch Klassifikationsgesellschaften
anerkannte Dichtigkeitsprüfung der Luken und weitaus weniger personal- und zeitaufwendig als die erst genannte Version. Hierzu wird ein
Ultraschallsender in der Luke positioniert und mit einem Suchgerät werden die
Lukenabdeckungen, bzw. deren Dichtungen abgesucht. Leckargen werden durch den Empfänger durch ein akustisches und optisches Signal gemeldet. Dieses Art der Dichtigkeitsprüfung erfreut sich auch bei den Schiffsleitungen einer
hohen Akzeptanz, so dass einige Schiffsleitungen nach erfolgreicher Prüfung ihres Schiffes sich dies durch den Sachverständigen schriftlich bestätigen lassen.
Sofern Leckargen festgestellt wurden, müssen diese möglichst vor
Ladebeginn, aber spätestens vor Auslaufen des Schiffes beseitigt werden. Wird die Dichtigkeit mit dem Wassertest geprüft, kann auf keinem Fall sofort mit der Beladung begonnen werden, da bei einer erfolglosen Nachbesserung der Dichtigkeit das Seewasser, welches beim Test verwand wird, in die Luken eindringt und somit die Ladung direkt nach deren Übernahme mit Seewasser kontaminiert.
Beide beschriebenen Verfahren können nur die Dichtigkeit der Lukendeckel während des Ruhezustandes des Schiffes attestieren. Dadurch, dass sich das Schiff im Seegang durch Hoggin, Sägging, Torrosion, verwindet und bewegt, können ebenfalls Undichtigkeiten hervortreten, die nicht im Hafen bzw. im Ruhezustand entdeckt werden können.
Die ersten beiden Abbildungen zeigen Besatzungsmitglieder beim
Abspritzen der Lukendeckeldichtungen mittels Seewasserschläuche. Einmal müssen die Lukendeckel gegen den jeweils nächsten Lukendecken abdichten (siehe Bild 1) und auf den Luken selbst. Besonders kritische Punkte sind die Übergänge von der Dichtung Lukendeckel / Lukendeckel zum Lukensüll. Wichtig ist für die Prüfung der seefeste Verschluss der Lukenabdeckungen.
Die Abbildung 3 zeigt die
Führung des Dichtungsgummis von der Horizontalen in die Vertikale beim
Übergang von der Dichtung Lukensüll / nächster Lukendeckel. Durch das
Öffnen und Schließen der Lukendeckel werden diese
"Übergangsecken" sehr stark mechanisch beansprucht, so dass es
teilweise, wie im nebenstehenden Bild zu sehen, schon zur Zerstörung des Dichtungsgummis kommt. Des weiteren ist auf der Abb. 3 eine Leckarge am „Stoß“ zweier Dichtungsgummis zu erkennen. Grundsätzlich sind Stoß- bzw. Ansatzstellen von Dichtungsgummis problematisch. Diese müssen mit
hohem Druck und einer gewissen Vorspannung eingesetzt werden, damit sie durch die mechanischen Beanspruchungen nicht zu Leckargen führen. Im Bereich von Umlenkungen und Ecken sind diese Stöße grundsätzlich zu vermeiden, da hier Spannungen im Dichtungsmaterial auftreten und früher oder später nahezu planmäßig zu Leckargen führen.
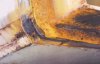
Abbildung 3 |
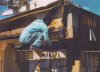
Abbildung 4 |
|
Die Abb. 4 zeigt ein
Besatzungsmitglied, welches in dem vor benannten Risikobereich
(Übergang von Lukendeckel zu Lukensüll) Dichtungseinheiten
auswechselt. Das Dichtungsgummi der Lukendeckel drückt auf dem
Lukensüll auf metallene Wülste. Das Eindrücken dieser Wülste in
die Gummidichtung gewährleistet den eigentlichen Dichtungsefekt. |
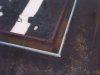
Abbildung 5 |
|
Durch ihre exponierte Lage
können sie nur unzureichend vor Korrosion geschützt werden und
bedürfen daher einer intensiven Pflege. Bei der Überprüfung der
Dichtigkeit stehen sie ebenfalls im Focus des Sachverständigen. Die
Abb. 5 zeigt einen intakten Dichtungswulst. |
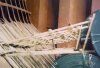
Abbildung 6 |
|
Insbesondere in den
Bereichen Luke 1 und 2, in denen sich das Schiff zum Steven hin
verjüngt, aber auch durch die "schrägen" Bordwände in
Bulkcarriern ist es problematisch, eine seitliche Ladungssicherung
herzustellen. Die Abb. 6 zeigt den Versuch einer formschlüssigen
Ladungssicherung zur Seite durch Pallhölzer. |
Für die erhebliche Masse der Coils sind die Hölzer deutlich zu schwach, des weiteren stützen sich die Hölzer nur an den Schrägen der Bordwand ab und würden bei der ersten Belastung nach oben weg gedrückt werden. Diese Art der Auspallung ist als reine Materialverschwendung zu bezeichnen.
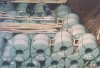
Abbildung 7 |
|
Das Bild 7 zeigt einen
sehr unregelmäßigen Stau. Die Coils sind nicht "sauber" im
Sattel geladen und es wurde kein explizites Locking-Coil verwendet.
Die Auspallungen zwischen den einzelnen Coils bieten kaum einen
Ladungssicherungseffekt. Bei der ersten seitlichen Bewegung eines
Coils würden diese "Ladungssicherungen" nach oben
herausgedrückt. |
Grundsätzlich sind Auspallungen bei der Verladung von Coils nur zwischen den einzelnen Tiers zu verwenden. Pallungen, die zwischen den Rundungen der Coils eingesetzt werden, bergen 1. die Gefahr der Verletzung der ersten Blechlage und können 2. können diese nur sehr unzureichend gefertigt
werden, da sie, wenn sie wirkungsvoll sein sollen, im Schwerpunkt der Coils angreifen müssen. Zusätzlich kann eine Auspallung nur wirksam sein, wenn eine geschlossene Formschlusskette bis zu den Bordwänden sicher gestellt ist. Dies ist im o.g. Bild ebenfalls nicht der Fall.
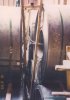
Abbildung 8 |
|
Das Bild 8 zeigt den Blick
zwischen zwei Tiers von warm gewalzten Coils. Zwischen den Coils wurde
der Versuch unternommen, mit Pallhölzern eine Ladungssicherung
herzustellen. Der Versuch ist als äußerst mangelhaft zu bezeichnen.
Die "Steher" (senkrecht gestellte Vierkanthölzer zwischen
den Coiltiers) scheinen war- und planlos zwischen die Coils gestellt
zu sein. Die gewählten Pallhölzer sind viel zu schwach und die
Aussteifungen falsch bzw. ungenügend platziert. Sinnvoller wäre es,
zwischen die einzelnen Coils Vierkantbalken (Formate von mind. 10 x 10
cm) einzuhängen, so dass das Holz stirnseitig eine Belastung erfahren
kann. |
Handelt es sich um standsichere Coils können die Pallhölzer in die Coilaugen eingehängt werden, sind es kippgefährdete Coils so lassen sich die Pallhözer auch in den Sattel einhängen. Nur im Schulterbereich des Staus müssen diese separat fixiert werden.
Das zur Ladungssicherung verwandte Holz (meist Nadelholz: Fichte, Tanne) ist auf der Faser mit ca. 30 daN/cm2 (30 kg/cm2) und auf der Stirnseite mit 200 daN (kg/cm2) zu belasten. Allein durch die Tatsache, dass die in der Abbildung verwandten Steher faserseitig belastet werden, wird die Wirkung um den Faktor 7 reduziert. Dazu kommt, dass das verladene Coil schon in der Peripherie teilweise teleskopiert ist und dadurch „eine scharfe Kante“ gebildet hat. Der eingesetzte Steher würde bei der geringsten Belastung brechen. Eine sinnvolle und materialsparendere Alternative wäre, 4 der
abgebildeten Balken zu bündeln und diese mit einem Brett zwischen die
Coilaugen einzuhängen. Mit dieser Vorgehensweise wären bei einer geschätzten Kantenlänge von 10 x 10cm, die durch eine Bündelung zu erreichen wäre, ein Ladungssicherungseffekt von 100 cm² x 200 daN = 20.000 daN = 20.000 kg entspr. 20 t erreich worden. Die in der Abbildung zu sehende „Aussteifung“ hält wahrscheinlich nur wenigen hundert Kilogramm stand. Die Abb. 9 zeigt die gleichen Fehler. Auch hier wurden Steher eingesetzt, die die Ladungssicherungswirkung herabsetzen.
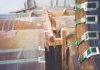
Abbildung 9 |
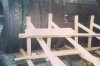
Abbildung 10 |
|
Die Abb. 10 zeigt die
Ladungssicherungsversuche durch Pallhölzer ein seitliches Verrollen
der Coils zu verhindern. Zwar greifen hier die Pallhölzer ungefähr
im Schwerpunkt an, doch stützen sie sich abermals nur an der schrägen
Bordwand ab. Hierdurch ist ihre Wirkung nahe Null. |
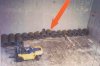
Abbildung 11 |
|
Die Abb. 11 zeigt einen
rechteckformatigen Schiffsladeraum. Auf dem Doppelboden (Schiffsboden)
wird ausreichend Stauholz verwandt. Das in der Mitte eingesetzte
Locking-Coil sitzt viel zu tief. Ein Locking-Coil darf nur bis zu 1/3
"einsinken". Bei weiterem Einsinken werden die seitlichen Kräfte
zu groß und es besteht die Gefahr der Ovalisierung der beteiligten
bzw. nachbarten Coils. |
An den Bordwänden wurde äußerst sparsam Stauholz eingesetzt. Dieses birgt besondere Gefahren. Im Seegang (bei seitlicher Schräglage des
Schiffes) „stützen“ sich alle Coils an der Bordwand ab. Der Druck auf dem
Stauholz (in der Abb. wurden Rechteckformate verwandt) wird erheblich. Da hier nur die Faser belastet wird, ist davon auszugehen, dass das Holz gequetscht bzw. zerquetscht wird. Hierdurch werden mehrere cm Raum gewonnen, so dass im vorliegenden Fall das zu tief sitzende Locking-Coil evtl. ganz
durchfällt. Dies gilt es, unbedingt zu vermeiden. Der im Vordergrund zu sehende Stapler verwendet einen Coildorn, welches wiederum zu begrüßen ist.
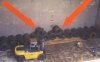
Abbildung 12 |
Nach der Intervention des Sachverständigen wurde die Stauung der Coils in der ersten Tier verbessert. Dadurch das die große Ladelücke auf zwei Lücken aufgeteilt wurde, konnten 2 Locking-Coils verwandt werden, die jetzt nur zu ca. 1/3 zwischen die anderen Coils „einsinken“. Hierdurch ist gewährleistet, dass genügend Sicherungskräfte zu den Seiten auftreten und die Gefahr der Ovalisierung ist gebannt. Der Einsatz des Stauholzes an den Bordwänden muss noch verbessert werden.
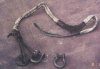
Abbildung 13 |
|
Die Abb. 13 zeigt einen
Drahtstropp, der als Anschlagmittel für die Coils verwandt wurde. Die
Umwicklung des Drahtes mit Tauwerk bringt keine tatsächliche
Verbesserung. Als Anschlagmittel für Coils ist derartiges
Anschlagmaterial abzulehnen. Er wurde auf Beteiben des Sachverständigen
aus dem Verkehr gezogen. |
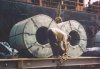
Abbildung 14 |
|
Die Abb. 14 zeigt kaltgewalzte Stahlbleche in Coils auf einem Lkw, der diese mittels Langgliederketten gesichert hat. Langgliederketten bergen an den Umlenkpunkten die Gefahr von Einkerbungen am Coil. Zur Ladungssicherung sind deshalb ausschließlich Kurzgliederketten zu verwenden. Als optimal ist der Schutz der Ladung dann zu
bezeichnen, wenn die Kurzgliederketten noch mit Schutzschläuchen versehen sind. Erst dann ist eine Schädigung der Kanten des Coilauges auch im
Belastungsfall ausgeschlossen. |
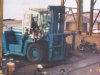
Abbildung 15 |
|
Die Abb. 15 zeigt einen Stapler mit Coildorn. Leider gehört dieses Anbaugerät nicht zur Standartausrüstung vieler Häfen dieser Welt. Auch lässt dieser Dorn die Abpolsterung des Gerüstes und des Dorn selbst durch Polyuhrethan-Beschichtungen vermissen. |
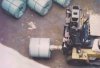
Abbildung 16 |
|
Die Abb. 16 zeigt für viele Häfen insbesondere in Südostasien den
Normalfall. Entweder wird eine breite Gabel des Staplers mit Holz belegt und dann mit Tauwerk umwickelt oder 2 schmalere Gabeln werden
zusammengeschoben, um sie dann mit Holz zu belegen und mit Tauwerk zu
umwickeln. |
Diese Art der "Schadenverhütung" kann ausreichend sein, muss aber kontinuierlich überwacht und nachgebessert werden. Die erheblichen Belastungen durch das Anheben der Coils mit dieser Hilfskonstruktion schädigen diese sehr Schnell und ein Nachbessern wird erforderlich.
Erfahrungsgemäß werden die Schutzeinrichtungen nicht regelmäßig kontrolliert und nachgebessert, sobald der Sachverständige die Luke verlassen hat. Häufig wirkt hier die alleinige Anwesenheit eines Vertreters des Kunden bzw. des Versicherers schadenverhütend.
|
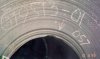
Abbildung 17 |
|
Auch warmgewalzte Stahlbleche in Coils sind gegen derartige Belastungen nicht immun. Das Bild 17 zeigt die Schädigung der Außenkante eines Coilauges durch Umschlagsgeschirre. Wahrscheinlich hat diesen Knick eine nicht abgepolsterte Gabelstaplergabel verursacht. |
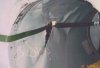
Abbildung 18 |
|
Die Abb. 18 zeigt die Folge von nicht oder nur ungenügend abgepolsterten Umschlagsgeräten. Die Verpackung des kaltgewalzten Stahlblechcoils ist zerstört und damit ist auch ihre korrosionsschützende Wirkung zunichte gemacht. Des weiteren ist ein mechanischer Schaden auf der Coilinnenseite höchst wahrscheinlich. Darüber hinaus sind am oberen Bildrand die Schädigungen der Staplergabeln zu erkennen. Wahrscheinlich ist der Stapler schräg in das Coilauge eingefahren und hat hier die Verpackung zerstört. Raues Handling gepaart mit falschen Anbaugeräten oder Anschlagmitteln verursachen erhebliche Schäden. |
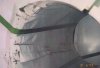
Abbildung 19 |
|
Das Bild 19 zeigt sehr eindrucksvoll, mehrere Knickkanten, hervorgerufen durch die Staplergabel. Mit Sicherheit sind hier einige Lagen Blech zerstört und wahrscheinlich sogar die Verpackung, so dass das Coil neben den mechanischen Schäden auch Korrosionsschäden zumindest durch Kondenswasser erleiden wird. |
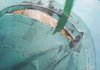
Abbildung 20 |
|
Die Abb. 20 zeigt wiederum einen Gabelschaden durch einen Stapler, hier wurde sogar das Verpackungsstahlband durchtrennt und die Verpackung zerstört. Die ersten Lagen des Stahlbleches sind zu erkennen und die Defor-mierung der Kanten ebenfalls. Viele weiterverarbeitende Betriebe lehnen derart beschädigte Rollen komplett ab, da mehrere Meter des Stahlbleches um das Coilinnenauge nicht mehr zu verwenden sind und somit der Arbeitsprozess unnötig früh unterbrochen wird. Diese Coils sind dann nur noch mit erheblichem Minderwert zu veräußern. |
Südostasien gehört zu den Regionen, in denen die vielfache Menge von Niederschlag während des Jahres fällt, als in unseren gemäßigten Breiten. Die Intensität der tropischen und subtropischen Regenfälle bedingt ein besonderes Augenmerk beim Schutz vor Niederschlägen. Auch voll verpackte Coils dürfen nicht mit Wasser in Berührung kommen.
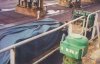
Abbildung 21 |
|
Die Abb. 21 zeigt, die bereit gestellten Coils kaltgewalzter Stahlbleche auf einem Lkw nur mit einer Plane abgedeckt. Bei Platzregen kann Wasser zumindest auf der Ladefläche unter die Plane gelangen, so dass die Coils mit „den Füßen“ im Wasser stehen Dies gilt es möglichst zu vermeiden. |
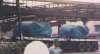
Abbildung 22 |
|
Die Abdeckung wie in Abb. 22 vorgenommen ist unzureichend. Da sie mit verschlissenen Planen vorgenommen wurde, besteht die Gefahr der Schädigung durch Regenwasser. |
Befindet sich der Liegeplatz des Schiffes, welches Stahl laden soll, in der Nähe von Massengutumschlagsanlagen, mit denen z. B. Kohle oder Düngemittel umgeschlagen werden, kann es zu erheblichen Kontermination durch die Stäube solcher Anlagen kommen.
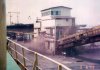
Abbildung 23 |
|
Die Abb. 23 zeigt eine erhebliche Wolke von Kohlestaub, die insbesondere auf unverpackten warmgewalzten Stahlblechen durch ihre Schwefelanteile erhebliche Korrosionsschäden verursachen können. Das gleiche gilt für den Umschlag von Düngemittel, die einmal als Reste auf der Pier zurückbleiben oder bei Umschlagsoperationen durch Staubverwehungen auf die Stahlladung
gelangen können. |
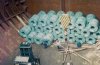
Abbildung 24 |
|
In der Abb. 24 ist ein Laderaum (Nr. 1 ganz vorn im Schiff) zu sehen, der für die Beladung mit Stahlcoils vollkommen ungeeignet ist. Die schräg nach vorn zulaufenden Bordwände erschweren den Aufbau einer geraden Tier extrem. Des weiteren muss ein Stau mit "runden Schultern" hergestellt werden. Da sich die unteren Coils gegen die Bordwand abstützen müssen, muss eine handwerklich einwandfreie Auspallung des trichterförmigen Holraumes
geschaffen werden. |
Da dieses in den seltensten Fällen möglich ist, sind solche Laderäume möglichst von der Beladung mit Coils auszuschließen. Zusätzlich sind die Belastungen durch Seegang in der Luke 1 besonders hoch und können in vertikaler Richtung bis 1 g betragen. |
Der Stau ist eher chaotisch und weist kein Locking-Coil auf.
Die Ladungssicherung von Coils ist vorzugsweise mit Stahlbändern
vorzunehmen. Der Vorzug von Stahlbändern ist, dass sie kaum über Elastizität verfügen (Elastizität kleiner 0,2 %) und sich auch im Gegensatz zu
Drahtseilverbindungen von Coil zu Coil herstellen lassen.
Ladungssicherung aus Drahtseilen hergestellt haben erstens den Nachteil, dass Drahtseile über weitaus mehr Elastizität verfügen als Stahlbänder und zweitens sind Drahtseilendverbindungen sehr zeit- und personalaufwendig in der Herstellung sind. Da Drahtseile mittels Spannschrauben gespannt
werden, müssen immer mind. 3 Coils zusammengefasst werden um den
erforderlichen Raum für eine Spannschraube zu schaffen. Eine Verbindung von nur 2 Coils ist daher nicht möglich. In der Abb. 24 sind alle sichtbaren Drahtseilendverbindungen äußerst mangelhaft ausgeführt.
Vorausgesetzt, dass es sich bei den Drahtseilen um Material mit 20 mm Durchmesser handelt, ist die Einsatzfestigkeit der Drahtseile selbst mit 16.000 daN entsprechen 16 t anzunehmen (Berechnung der
Einsatzfestigkeit: d x d x 40 nach Faustformel / Ladungssicherungshandbuch S. 43). Da aber nur 2 Drahtseilklemmen pro Drahtseilendverbindung verwandt wurden, ist damit zu rechnen, dass bei einer Belastung von 4 bis 6 t die Drahtseile durch die Drahtseilklemmen rutschen. Somit bedeutet diese Art der
mangelhaften Ladungssicherung zusätzlich noch eine erhebliche
Materialverschwendung. Die Einsatzfestigkeit der Drahtseilendverbindungen könnte durch das Aufsetzen von jeweils 2 weiteren Drahtseilklemmen pro Drahtseilendverbindung verbessert werden.
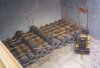
Abbildung 25 |
|
Abb. 25. In diesem ebenfalls rechteckigen Ladungssicherungsraum wurde ein Stau von warmgewalzten Stahlblechen in Coils (schwer bis sehr schwer) angelegt. Auch hier wurden die Drahtseilendverbindungen mangelhaft
ausgeführt (nur 2 Drahtseilklemmen je Drahtseilendverbindung). Die Auspallungen zwischen den Tiers könnten durch Einhängen von auf der Stirnseite belasteten Vierkanthölzern effektiver und materialsparender ausgeführt werden und die Verwendung des Stauholzes an den Bordwänden muss ebenfalls verbessert werden. |
In dieser Luke wurde ein Stapler mit zusammengeschobenen Gabeln verwandt, ohne dass diese auch nur im geringsten durch die Auflage von Holz und die Verwendung von Tauwerk geschützt waren. Die Schäden waren so vorprogrammiert.
|
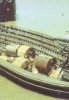
Abbildung 26 |
|
Abb. 26. Die Anlieferung von warmgewalzten Stahlcoils in einer offenen Barge zur Verladung auf ein Seeschiff auf Reede.
|
Grundsätzlich ist die Reede-Verladung als äußerst problematisch anzusehen:
- muss der Stahl meist an der Pier von Landfahrzeugen auf Bargen umgeladen werden,
- sind die Bargen häufig ungedeckt,
- bedingt die Ver- und Entladung in Bargen einen erneuten Handlingprozess, der ebenfalls schadenträchtig ist,
- kann es beim Transport auf die Reede und beim Verladen auf der Reede zu erheblichen Salzwasserkontaminationen kommen, des weiteren
bewegen sich zumindest die Bargen im Seegang teilweise erheblich, so dass es beim Anschlagen und Anheben der Coils zu Ramponagen
kommen kann.
|
Zurück zum Anfang