Foto des Monats – September 2019 |
[English version] |
„Letzte Ausfahrt…“
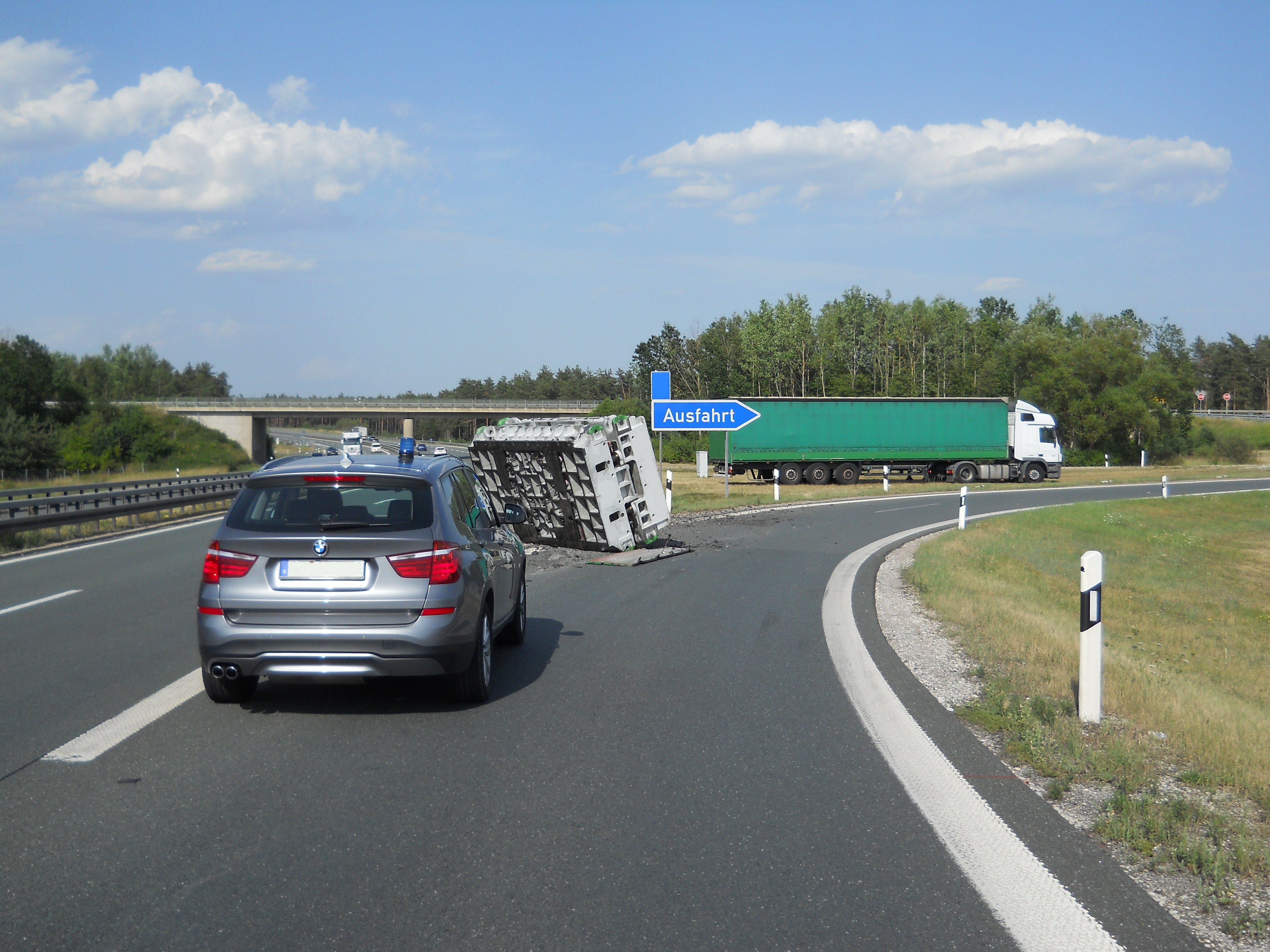
Abbildung 1 [VPI Amberg]
24,5t Stahl liegen auf einer Autobahnausfahrt. Es handelt sich um eine Blechpresse. Was für ein Glück, dass die Presse nicht gleich hier schon Blech gepresst hat, sondern nur Asphalt aufgekratzt, und der Fahrbahn so zu zwei kräftigen Schrammen verholfen hat.
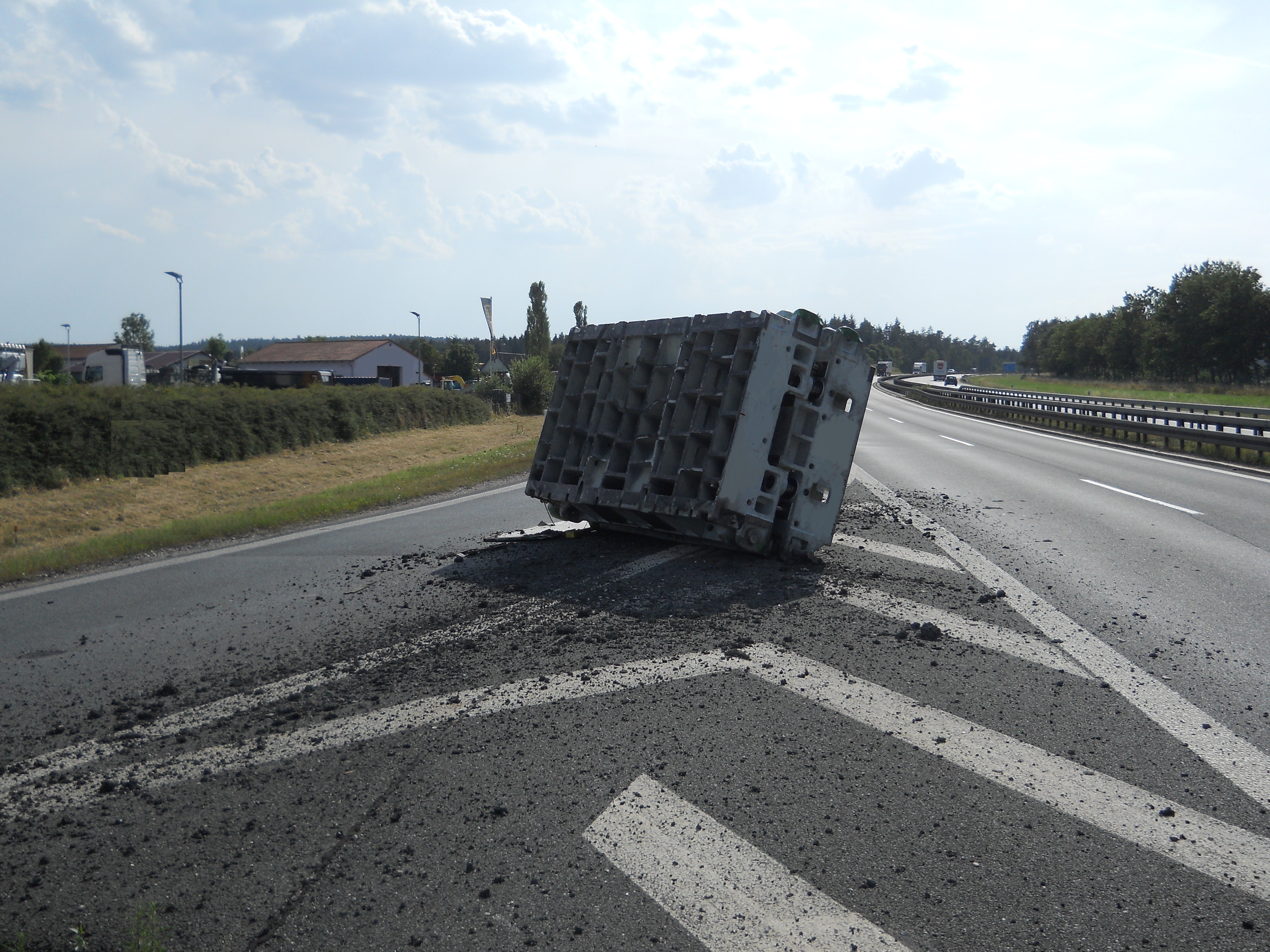
Abbildung 2 [VPI Amberg]
Diese Gegenlichtaufnahme (Abb. 2) zeigt sehr schön, dass der Aufschlag wohl recht kräftig gewesen sein muss, denn die Asphaltkrümel sind auf einer recht großen Fläche verteilt. Auf der Abb. 3 sind die tiefen Furchen in der Fahrbahn gut erkennbar.
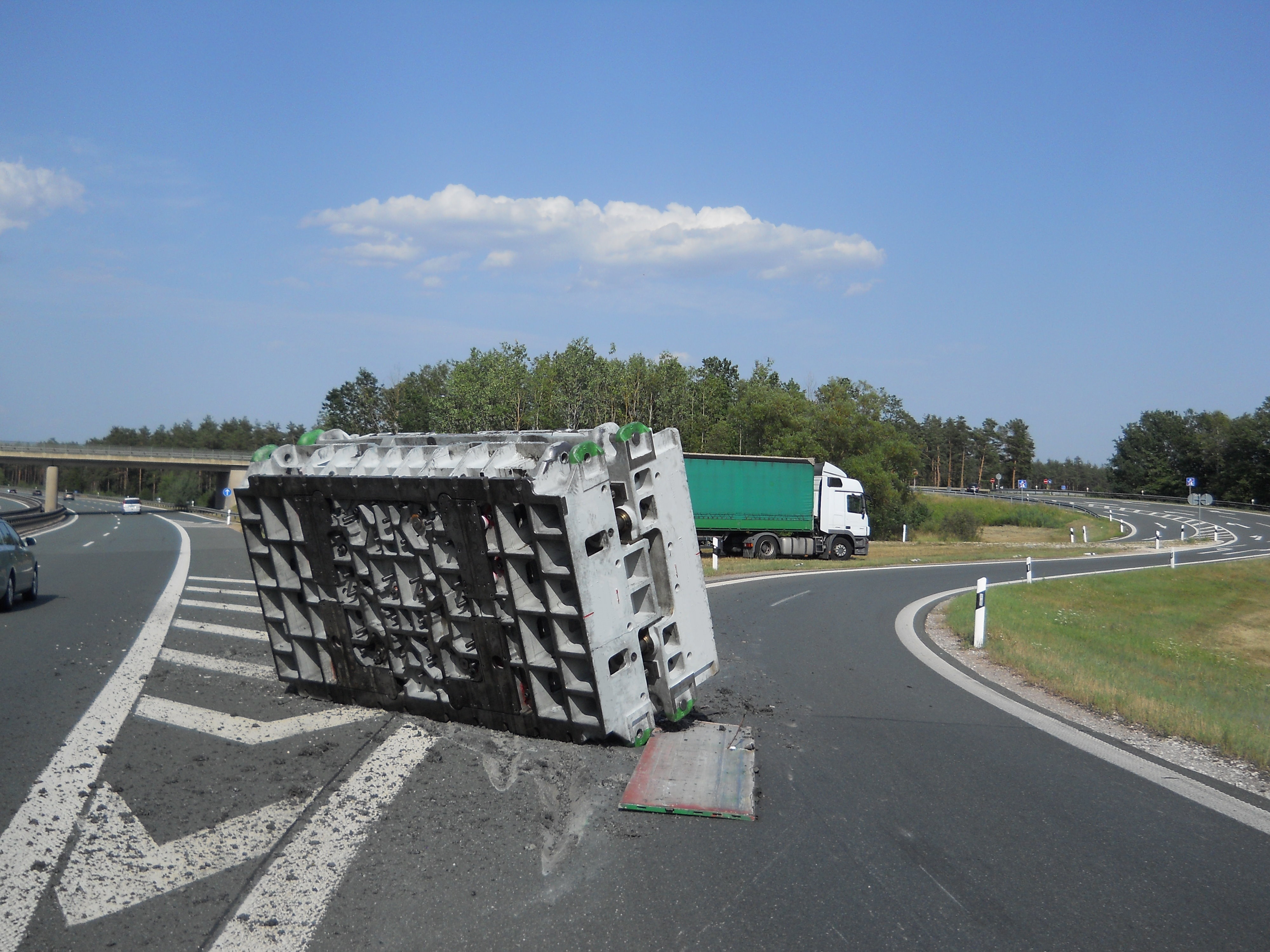
Abbildung 3 [VPI Amberg]
Was ist passiert? Die Ladung war offensichtlich schlecht gesichert. Der LKW ist mit etwa 50km/h in die Abfahrt eingefahren, so die Information der aufnehmenden Polizisten. Die Ladung ist mehr oder weniger geradeaus weitergefahren/-gerutscht.
Es war viel Glück im Spiel, denn es lag kein Auto unter der Presse. Die Fahrbahn ist beschädigt, das lässt sich schnell reparieren. Die Presse wird ein Totalschaden sein und damit wird ein Versicherer mehrere 100.000.-€ bezahlen müssen, und, wenn mit diesem Schaden noch eine Betriebsunterbrechung mit einhergeht, dann kann es richtig teuer werden. Nur damit es mal erwähnt wird, eine Betriebsunterbrechung kann sein, dass ein PKW-Werk aufgrund von fehlenden Blechteilen nicht weiterarbeiten kann. Schaden pro Tag ca. 150.000.-€. Die Zeit bis so eine Presse wiederbeschafft werden kann beträgt einen bis zwei Monate (mit Glück). Das macht bei 22 Arbeitstagen im Monat für zwei Monate schnell einen Schaden von 6.6 Mio. Euro.
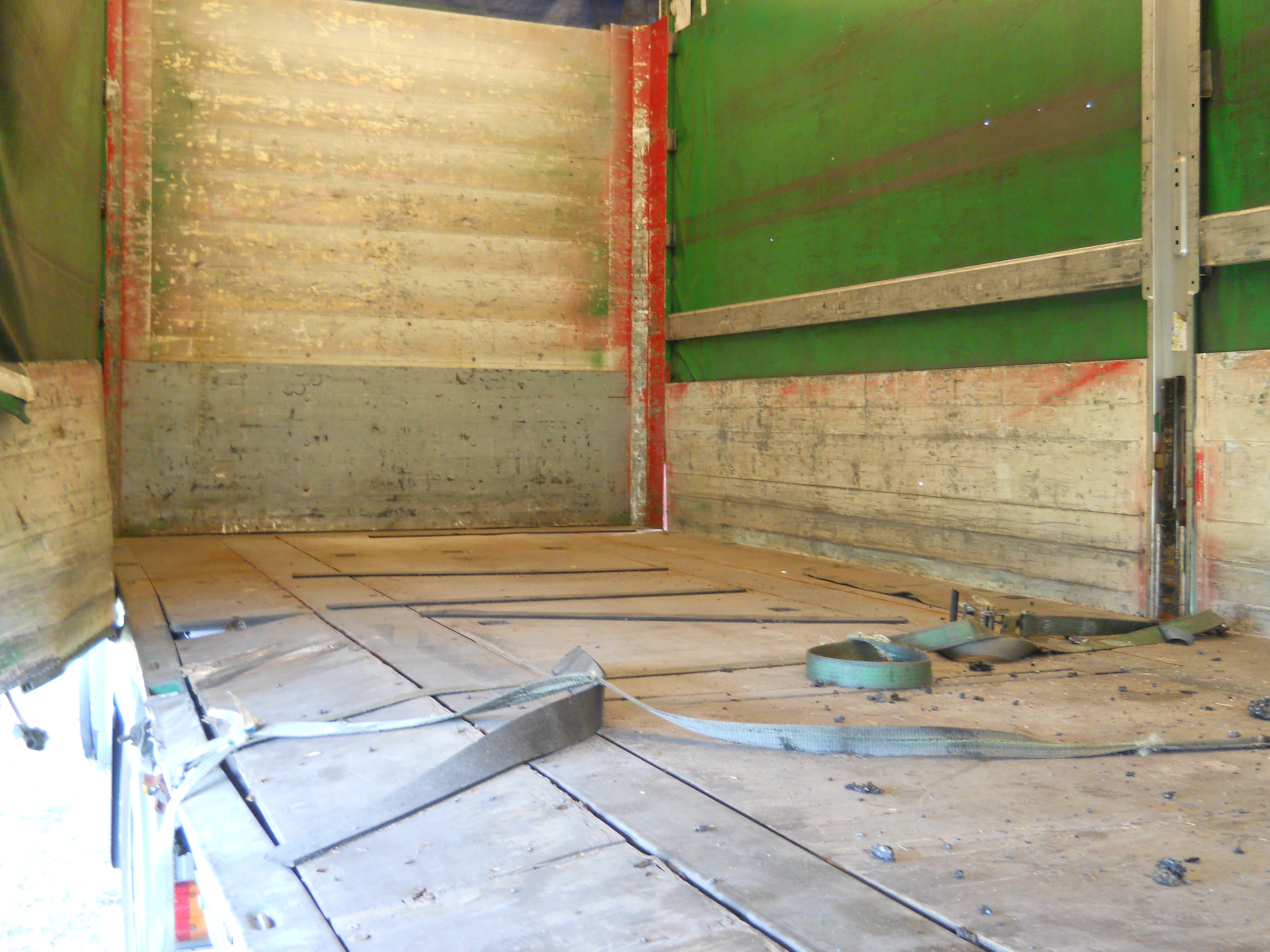
Abbildung 4 [VPI Amberg]
Die Presse war mit 4 Niederzurrungen und mit RH-Material „gesichert“. Derartige Massen mit Niederzurrungen zu sichern, ist vorsichtig ausgedrückt, nicht gerade ökonomisch sinnvoll, wenn überhaupt irgendwie machbar. Warum hat die Presse die Ladefläche so beherzt seitwärts verlassen, trotz rutschhemmender Matten?
Was wir hier in dieser Kolumne anstellen, sind sehr häufig Vermutungen, Reime die wir uns auf das machen, was wir aus den Bildern lesen, und was wir an Informationen haben. Aus der Abb. 5 lesen wir, dass sich neben einigen RH-Matten auch noch Gesteinsbröckchen (Schlacke, oder ähnlich) auf der Ladefläche befanden. Das bringt uns zu der Vermutung, dass die RH-Matten nicht so wirken konnten, wie sie sollten. Die Ladefläche war nicht besenrein, was dazu führt, dass wir nur einen Reibwert von maximal μ = 0,2 annehmen können. Somit konnte die Presse mit so viel Energie gegen die Bracken (das sind die Ladebordwände) rutschen, diese durchbrechen, und auf die Straße stürzen.
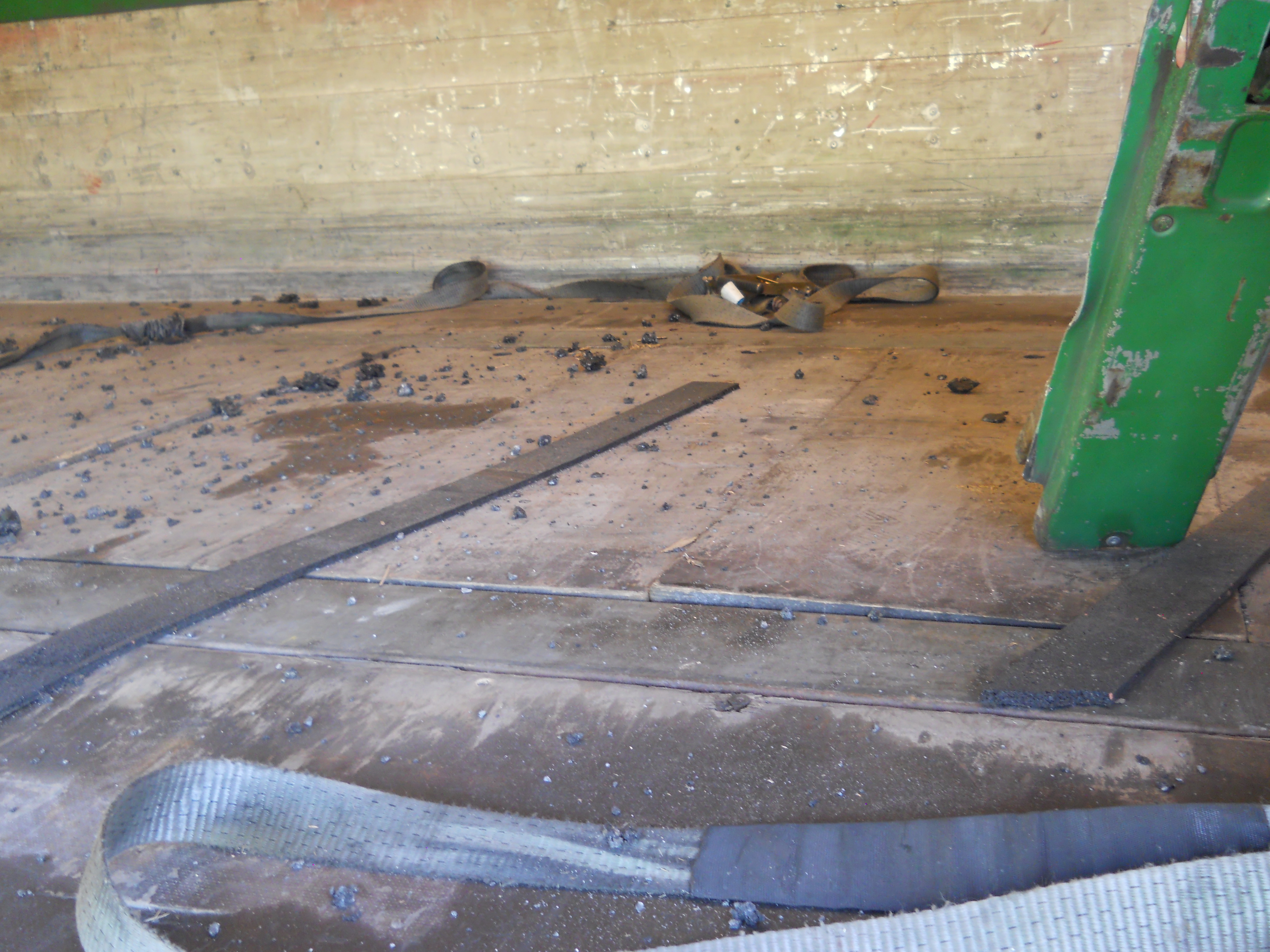
Abbildung 5 [VPI Amberg]
Grundsätzlich lässt sich die seitliche Ladungssicherung zu 100% mit Reibungserhöhung bewerkstelligen. Die nötige Mindestsicherung dafür war in Form von Niederzurrungen angebracht. Logische Folgerung bei Besichtigung des Fotos: Die Presse war durch den unsauberen Ladeboden reibungstechnisch nicht ausreichend von der Ladefläche getrennt.
Warum im ersten Viertel der Ladefläche so viel RH-Mattenstreifen liegen erschließt sich uns nicht. Vielleicht wären sie unter der Presse besser aufgehoben gewesen. Zuvor hätte die Ladefläche sauber gefegt werden müssen. Nur dann können die RH-Matten ihre Aufgabe auch erfüllen.
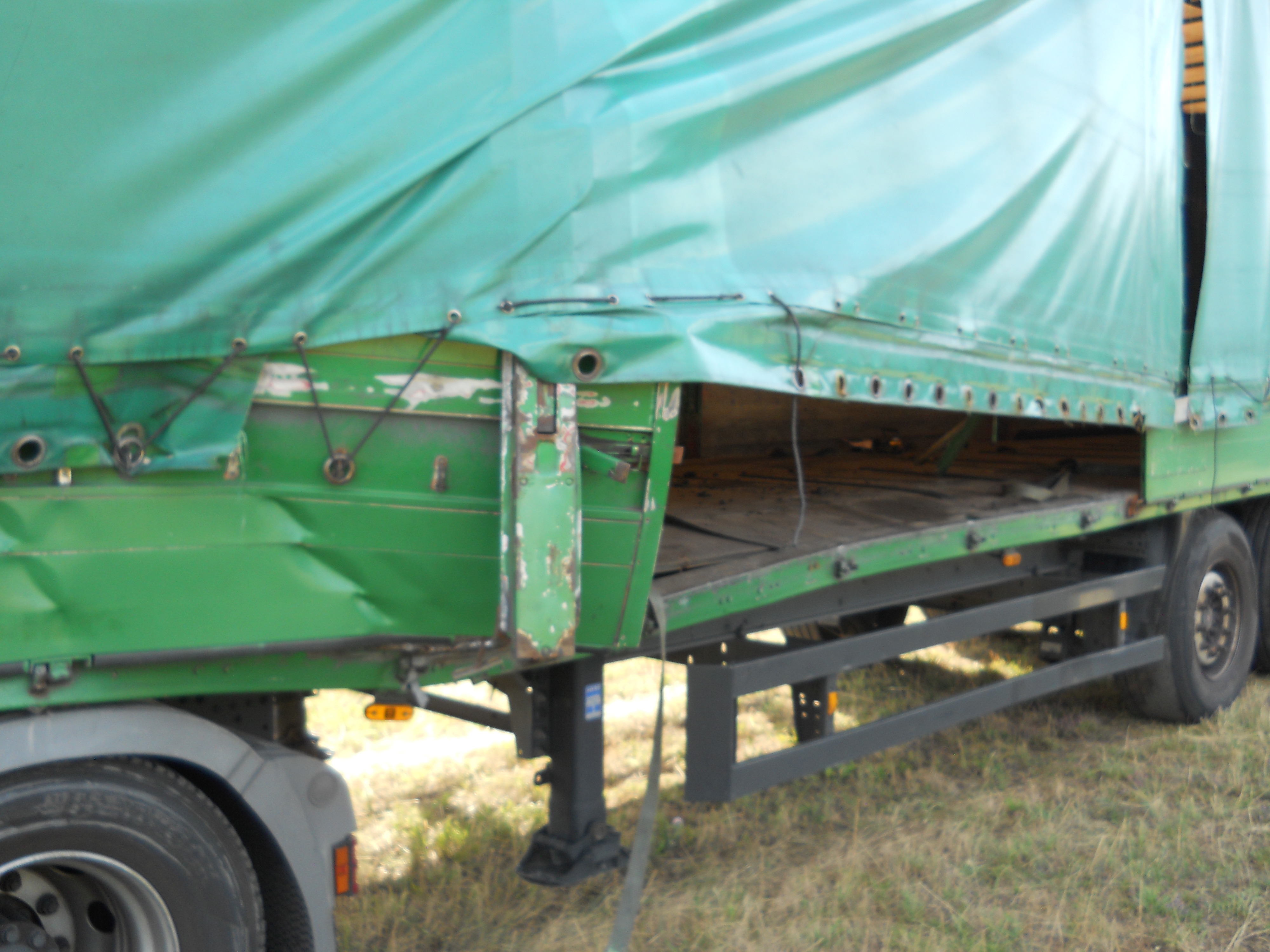
Abbildung 6 [VPI Amberg]
Die Abb.4 lässt erkennen, dass die Presse nahezu im 90°-Winkel zur Seite gerutscht ist. Sind solche Massen erstmal in Bewegung, ist die kinetische Energie derart hoch, dass weder eine Bordwand, noch Klapprungen (Abb. 6), einen nennenswerten Widerstand bieten können.
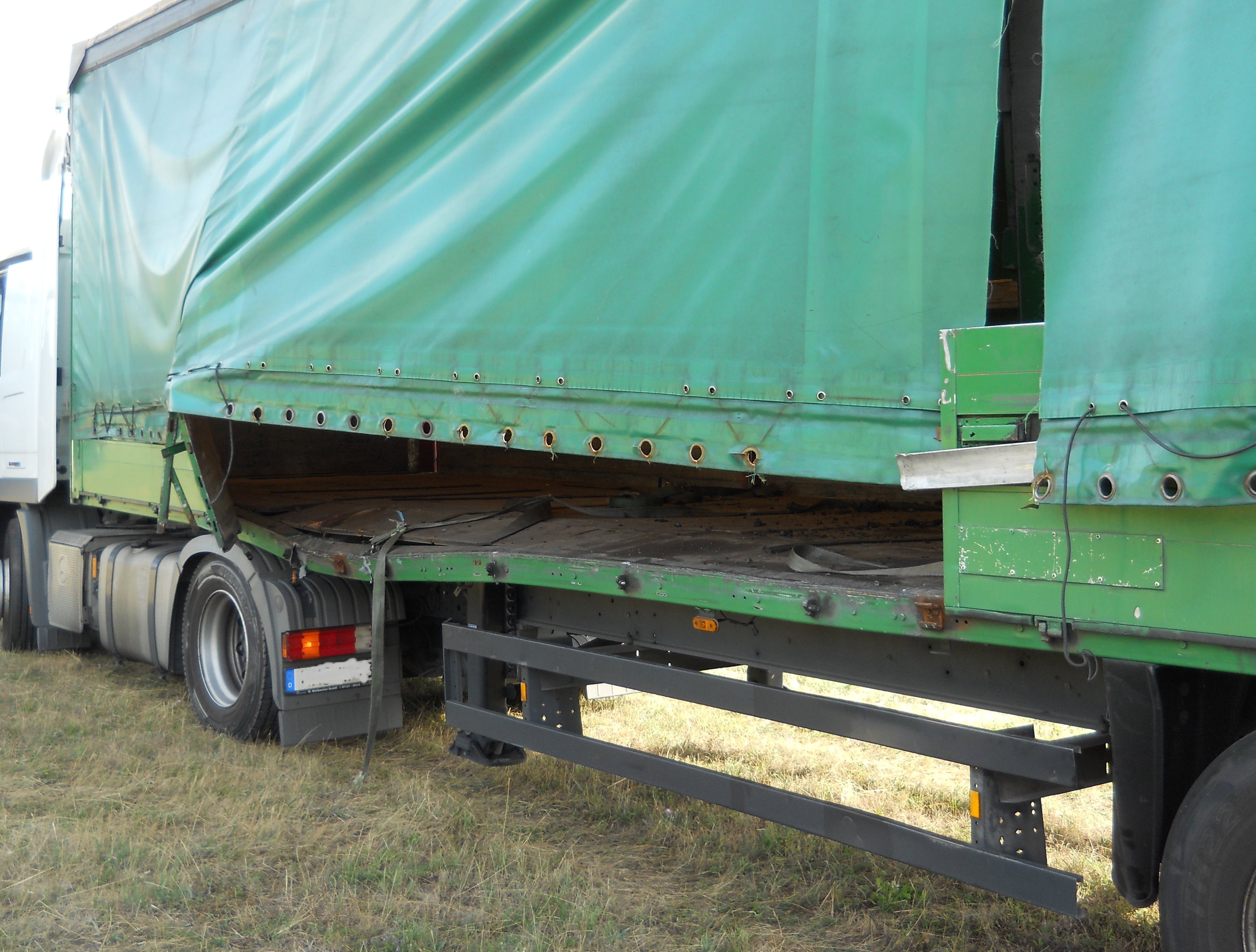
Abbildung 7 [VPI Amberg]
Auf der Abb. 7 gut zu erkennen, eine Ladebordwand ist herausgebrochen. Sie liegt jetzt unter der Presse auf der Fahrbahn (Abb.3). Die vordere Bracke ist stark deformiert. Ebenso ist die Ladefläche stark nach unten verbogen.
Ladungssicherung
Ob die Presse richtig auf dem Fahrzeug positioniert war, können wir nicht sagen. Was genau unter der Presse lag, auch nicht. Wir nehmen an RH-Material, aber leider nicht ausreichend, bzw. zusammen mit Gesteinsbröckchen. Wie lässt sich so eine Ladung reibungstechnisch von der Ladefläche trennen?
Zunächst wird die Ladefläche mit einem Besen (besenrein) gesäubert.
Wir nehmen fünf oder sechs bohlenformatige Hölzer, belegen sie von beiden Seiten vollflächig mit RH-Material und positionieren darauf die Presse. Es sollten hier durchvulkanisierte RH-Matten verwendet werden. Die auf den Fotos erkennbaren Matten sind Granulatmatten, die bei sehr schweren Gütern nicht immer die beste Wahl sind.
Die vier Gurte, die hier als Niederzurrungen eingesetzt wurden, hätten wir lieber als Umspannungen gesehen. Zwei von jeder Seite genutzt (Beschreibung ähnlich, wie im letzten Foto des Monats „Der Jackknife-Effekt oder ein Grabstein auf der Suche nach seinen Kunden“). Sie geben der Reibung durch ihren Niederzurrungsanteil die nötige Sicherheit und sichern die Presse selbst pro Seite zusätzlich mit ca. 8.000 daN. Das „ca.“ bezieht sich auf den Winkel den wir nicht berücksichtigen können (Cos Alpha ½). Voraussetzung ist, dass jedes Gurtende auf einem LS-Punkt ruht und, dass sie über Kantenschoner geführt werden, die über die Kanten der Presse gelegt werden.
Nach vorne fehlen noch 4.900 daN an Sicherungskraft. Auch hier würden wir mit zwei Kopfbuchten oder Umspannungen arbeiten. Die Presse ermöglicht, so wie wir es sehen, die Sicherung durch Direktzurrungen (siehe rote Kreise in Abb. 8), angelegt an den Anschlagpunkten oben an der Presse.
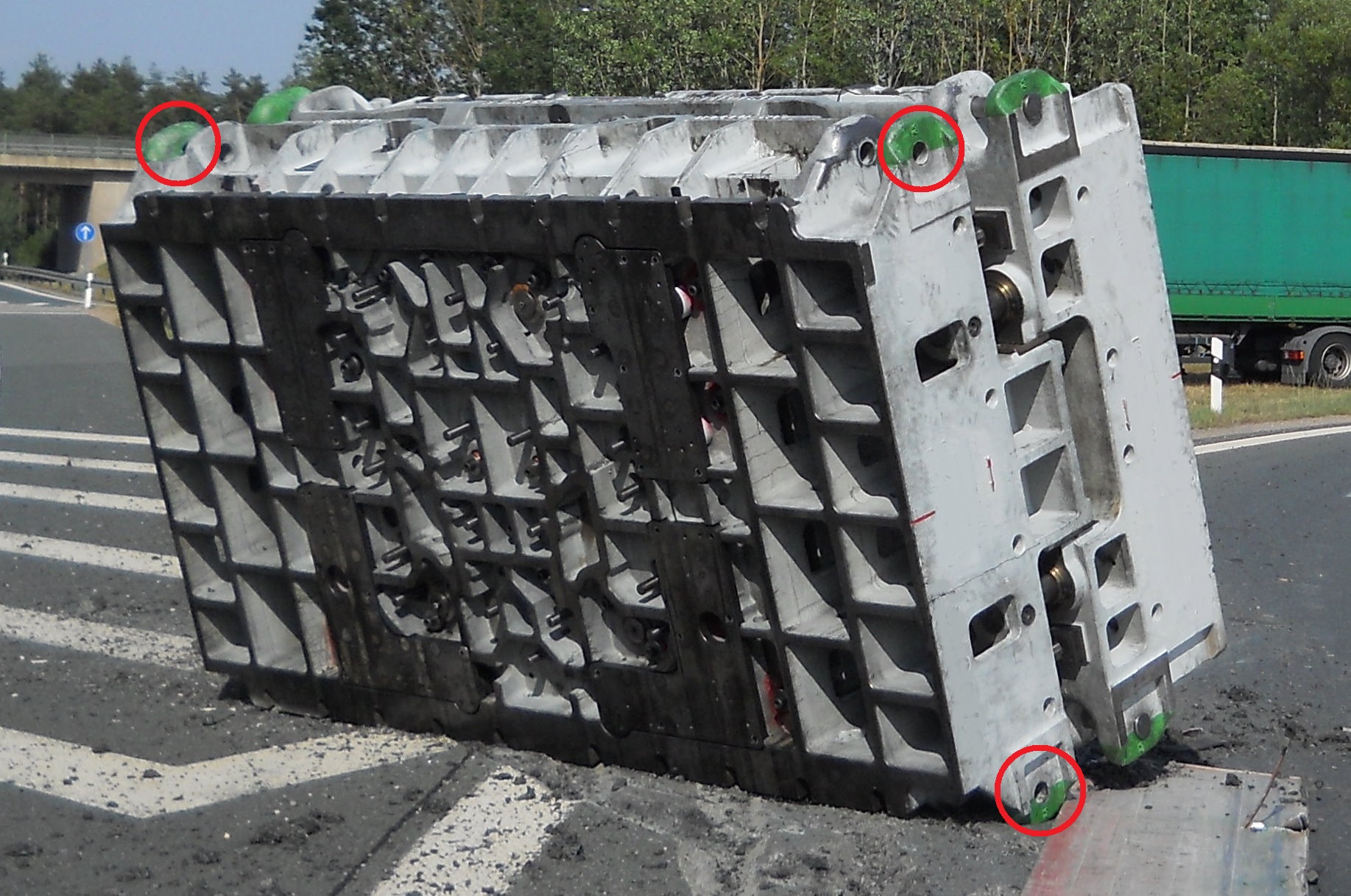
Abbildung 8 [VPI Amberg]
Die Geeignetheit sollte der Hersteller der Presse gewährleisten. Es sollte auch in seinem Interesse liegen, dass dieses fast 400.000 Euro teure Werkzeug sicher am Bestimmungsort ankommt. Diese Sicherung ist unsere erste Wahl. Die Sicherungsmittel sollten möglichst gleich lang sind, damit sie nicht unterschiedlich belastet werden. Die statische Unbestimmtheit lässt grüßen. Es geht immerhin um 24,5t Stahl und nicht um einen Block Polystyrol.
Verantwortung:
Zum guten Schluss sei noch ein Wort zur Verantwortung erlaubt. Zum Fahrer wurde schon einiges erwähnt, zum Verlader noch nicht. Der Spediteur bzw. der Frachtführer, der Fahrer und der Verlader teilen sich die Verantwortung für die Ladungssicherung. Da der Fahrer noch nicht einmal im Besitz einer gültigen Fahrerlaubnis war, ist fraglich ob er einen Ladungssicherungskurs besucht hat, denn nur dann ist er in der Lage eine derartige Ladung verantwortungsvoll zu sichern. Für die Auswahl des Fahrers ist der Halter verantwortlich. Er muss prüfen, ob der Fahrer eine gültige Fahrerlaubnis hat und ober er in der Lage ist, das Fahrzeug sicher zu führen. Ebenso ist er dafür verantwortlich, dass der Fahrer eine Berufskraftfahrerqualifizierung durchlaufen hat. Auch dies würde in einem gültigen Führerschein vermerkt.
Was den Verlader angeht, können wir nur den Kopf schütteln. So eine Presse wird sich der Fahrer nicht selbst aufgeladen haben, um sich dann unbemerkt aus dem Staube zu machen. Vielmehr wird die Presse mit einem Kran verladen worden sein und dann wurde der Fahrer mit der Ladungssicherung alleine gelassen. Der Verlader trägt aber Verantwortung für die Ladungssicherung, er kann diese zwar auf den Fahrer übertragen, muss aber kontrollieren ob dieser die Sicherung auch richtig ausführt. Zum einen geht von 24,5t eine hohe Gefahr aus und zum anderen könnte man von einem Verlader, für eine Ladung, die knapp 400.000 Wert hat, ein bisschen mehr Engagement erwarten. Nur um es klarzustellen: Auch wenn die Ladung nur einen geringen Wert und ein geringes Gewicht hat, trägt der Verlader die Verantwortung mit.
Wäre durch diese Presse jemand zu Schaden, oder zu Tode gekommen, hätte ein Richter die Verantwortung bei allen drei Beteiligten geprüft. Beim Verlader trägt die Verantwortung die Geschäftsführung (wenn diese nicht verantwortungsvoll delegiert wurde). Ergo hätte die Frau oder der Herr Geschäftsführer(in) neben dem Fahrer auf der Anklagebank Platz genommen. Sicher ein sehr unangenehmes Gefühl.
Die Ladungssicherungskolumnisten wünschen Ihnen allzeit eine ladungssichere Fahrt!
Zurück zum Anfang