Foto des Monats – Januar 2009
|
[English version] |
Gurtsegen
Betrachtet der gemeine Ladungssicherungsinteressierte dieses Bild, müsste er spontan annehmen, dass ein wie auch immer gearteter Ladungssicherungskolumnist doch spontan in Begeisterungsstürme ob der Vielzahl der verwendeten Gurte ausbrechen müsste. In der Tat ist das Fahrzeug bzw. große Teile des gesamten Unternehmens zukünftig reich mit Gurten gesegnet. Diese Ladungs-I-Träger (wir gehen mal von 24 t aus, da das genaue Gewicht nicht überliefert ist) war mit nur sechs Niederzurrungen (die sechs orangenen Gurte im Vordergrund) "gesichert".
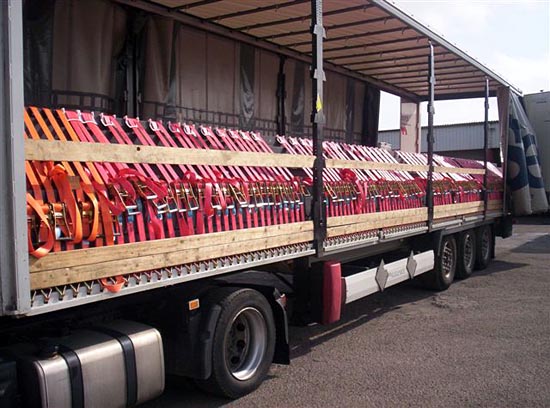
Abbildung 1 [Klaus Brändle]
Bei einer LKW-Kontrolle stellten die Beamten vollkommen textsicher fest, dass diese Sicherung in der Tat unzureichend war. Ob die Beamten oder der Fahrer auf dem Prinzip der Niederzurrung beharrten, ist nicht überliefert. Fakt ist aber, dass niedergezurrt wurde. Bevor aber dieses Denkmal an die Niederzurrung umgesetzt wurde, wurde gerechnet. Diese Rechnung ergab, dass soweit dann unbedingt tatsächlich über das Prinzip der Niederzurrung eine Ladungssicherung hergestellt werden soll, 135 Gurte vonnöten gewesen wären.
Spätestens beim Erhalt des Rechenergebnisses hätten alle Beteiligten folgende Lehre daraus ziehen müssen:
Zur Sicherung von derart schweren Ladungen ist die Sicherungsart Niederzurren schlichtweg nicht geeignet.
Soweit dem Verfasser bekannt, sind derartige Fahrzeuge zwar zur Ladungssicherung exzellent geeignet, aber nicht alle Ladungssicherungspunkte im seitliche Profil dürfen gleichzeitig zur Ladungssicherung verwandt werden, sondern nur eine bestimmte Anzahl pro laufendem Meter. Sind alle Langhebelratschen, die allem Anschein nach hier verwandt wurden, voll gespannt, erreichen sie ggf. eine Vorspannung auf der Zugseite von jeweils 500 daN. Das macht in Summe bei 96 Gurten (mehr LS-Punkte waren nicht da) 49.000 daN nur auf der Zugseite. Geht man von einem K-Wert von 1,5 aus, kommen auf der rechten Fahrzeugseite immerhin noch 24.500 daN an Vorspannung an. Somit wird das Fahrzeug zusätzlich zu seinem Ladungsgewicht noch mit 73.500 daN belastet. Gesetzt den Fall, dass tatsächlich nur 24.000 daN an Gewichtskraft der Ladung mit im Spiel sind, wird der zarte Auflieger in diesem Moment mit 97.500 daN belastet. Ob er das aushält?
Dazu kommt noch, dass nicht nur die Ladefläche in der Mitte belastet wird, sondern auch der Fahrzeugrahmen an der Außenseite kräftig nach oben gezogen wird und somit die Ladefläche des Aufliegers wohl eher einer Badewanne gleicht, denn einer wirklichen planen Fläche.
Besonders gut zu sehen ist, da in Reih und Glied aufgereiht, dass alle Spannelemente auf der linken Fahrzeugseite angebracht wurden. Somit verteilt sich die Vorspannung extrem unterschiedlich, und im Belastungsfall würde die Ladung, wie im letzten Bild des Monats vom November 2008 gut zu sehen, sicherlich gerne auf die rechte Fahrzeugseite ausweichen, um dort "ihr Unwesen" zu treiben.
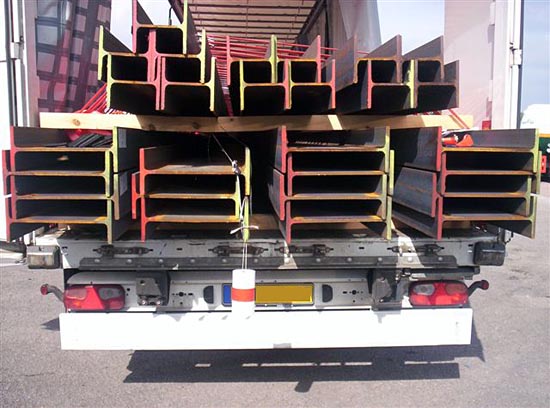
Abbildung 2 [Klaus Brändle]
Von hinten betrachtet wird das gesamte Ladungssicherungsdenkmal völlig ad absurdum geführt. Zwischen den zu einzelnen Paketen zusammengestapelten, aber nicht gebündelten I-Trägern sind "laut und deutlich" Ladelücken zu erkennen. Nun generieren Niederzurrungen grundsätzlich diagonal nach innen gerichtete Kräfte, die an den oberen äußeren Ladungsecken angreifen. Sobald sich dieses Fahrzeug in Bewegung setzt, würden die nicht unerheblichen Vorspannkräfte von immerhin 73.500 daN dafür sorgen, dass die Ladung zusammenrutscht. Da die Vorspannkräfte nun aber wie schon erwähnt inhomogen verteilt sind, würde die Ladung nach rechts rutschen.
Betrachtet man das Vierkantholz, welches von hinten zu sehen ist, lässt sich erahnen, wie selbiges unter der nahezu märchenhaften Vorspannung zu leiden hat. Schon im Stillstand des Fahrzeuges hat sich ob des Ladungsgewichtes und der immensen Vorspannung der Stahl kräftig in das Holz eingearbeitet. Wie lange das Vierkantholz über dem zweiten Stapel I-Träger von links auf der Ladefläche noch durchhält, kann nur eine Frage der Zeit sein.
Wie ist nur eine derartige Ladung vernünftig, wirtschaftlich, schnell und gut zu sichern?
![]() |
Zuerst sollten alle hölzernen Zwischenlagen entsprechend stabil und bitte in Bohlenformaten ausgelegt werden, denn wie schon so häufig erwähnt, unterstützen quadratische Querschnitte das Verrollen der Ladung. |
![]() |
Die Reibung ist immer ein wertvoller Gehilfe bei der Ladungssicherung. So sollte auch hier auf reibungserhöhenden Materialien nicht verzichtet werden. Sie müssen unter wie über den Hölzern ausgelegt werden, und zwingend ist darauf zu achten, dass ausschließlich schwerlastgeeignetes RH-Material verwandt wird, welches auch den entsprechenden Belastungen standhalten kann. |
![]() |
Sofern mit dem Stapler verladen wird, sollten Ladelücken zwingend unterbleiben. Erfordert eine Kranbeladung Ladelücken zwischen den einzelnen Stahlpaketen, können hier schon während der Verladung Vierkanthölzer eingepasst werden, gegen die geladen wird. Dadurch ist ein optimaler Formschluss herzustellen. |
Die seitliche Sicherung
Nun kann man sich Mühe geben, wie man will – die unteren vier Pakete werden immer breiter sein, als die oberen drei. Somit wird auch die Ladungssicherungsmethode Umspannung die einzelnen Pakete separat behandeln müssen. Wenn wir davon ausgehen, dass die vier unteren Pakete gemeinsam 14 t an Masse haben und zumindest unter den I-Trägern RH-Material Verwendung fand, sind die unteren Pakete mit jeweils zwei Umspannungen von jeder Seite gut seitlich zu sichern. Am besten lassen sich diese Umspannungen herstellen, wenn die Gurte vor der Verladung der zweiten Lage kleinerer Stahlpakete ausgelegt werden. Das Spannen kann dann nach Beendigung der Verladung erfolgen. Auch die zweite Lage kleinerer Pakete kann mit nur vier Umspannungen seitlich gut gesichert werden.
Der geneigte Leser mag nun feststellen, dass nur RH-Material unter den Trägern platziert werden konnte und nicht zwischen den Trägern und daher darf der gute Reibbeiwert nicht schlüssig für alle Träger angewandt werden. Richtig! Doch durch die Stapelung und Verzahnung der I-Träger ergibt sich nahezu eine Blockbildung. Nur in äußeren Bereichen könnten Träger auf Träger rutschen. Dies wird aber durch die Direktzurrung (seitlich) verhindert.
Sicherung in Längsrichtung
Da ob der vielen Gurte die Ladung nicht wirklich zu sehen ist, wird davon ausgegangen, dass es sich bei der Ladung um I-Träger handelt, die die gesamte Länge des Aufliegers in Anspruch nehmen. Ob Formschluss zur Stirnwand bestand, ist nicht überliefert. Auch wissen wir nicht, welche Belastung die Stirnwand in der Lage ist, aufzunehmen. Sicherheitshalberweise gehen wir davon aus, dass die Stirnwand maximal 5 t an Sicherungskapazität bietet.
Zuerst betrachten wir den unteren Ladungsstapel mit 14 t Ladungsgewicht. In Längsrichtung müssen wir beachten, dass nur die untere Lage, sprich vier I-Träger (ca. 3,5 t) Kontakt zu RH-Material haben. Bei dem RH-Material gehen wir von einem Reibbeiwert von 0,5 μ aus. Somit bleibt noch ein Sicherungsbedarf von 1.050 daN über. Die darüber liegenden 10,5 t haben auf den rostigen Träger einen Reibbeiwert von maximal 0,3 μ. Sicherheitshalber werden, da keine verlässlichen RH-Werte zur Verfügung stehen, nur mit 0,25 μ gerechnet. Somit sind für diesen Bereich noch 5.775 daN an Sicherungskraft erforderlich. Zusammengenommen wären dies 6.825 daN. Hiermit wäre die Stirnwand schon überfordert.
Folgende Lösung bietet sich an: Die beiden mittleren Pakete werden unter Zuhilfenahme von adäquater Lastverteilungsmaßnahmen an der Stirnwand direkt formschlüssig herangeladen. Bei den beiden äußeren Paketen belässt man eine Ladelücke von ca. 5 cm. Bedingt durch die Form der I-Träger können um die Stirnseiten der äußeren Pakete Umspannungen, sogenannte Kopfbuchten, genommen werden. Bedingt durch die Art der Verladung und die Form der Träger können diese Direktzurrungen einseitig erfolgen, d. h. sie müssen nicht diagonal über den gesamten Ladungsstapel geführt werden. Dies erleichtert die Zurrung deutlich. Um die Ladungspakete in der zweiten Lage zu sichern, muss entweder eine Holzbarriere gebaut werden, die dann mittels Umspannungen entsprechend abgefangen wird oder es müssen insgesamt sechs Umspannungen angebracht werden, um die Ladungssicherung nach vorne zu gewährleisten.
Anmerkung
Wären die I-Träger geschachtelt und stehend verladen worden, hätte jeder einzelne I-Träger Kontakt zu RH-Material erhalten und die Sicherung in Längsrichtung wäre deutlich leichter und einfacher auszuführen gewesen. Leider lässt das Material eine verschachtelte Verladeweise nicht immer zu.
Sicherung nach hinten
Wenn alle I-Träger Kontakt zu RH-Material haben, könnte man durch die Verwendung von drei bis fünf Niederzurrungen die Mindestsicherung sicherstellen und schon dann von einer ausreichenden Ladungssicherung sprechen. Dem Verfasser missfällt aber eine ausreichende Ladungssicherung. Eine gute wäre ihm schlichtweg lieber. Insofern empfehlen wir an dieser Stelle für die unteren Ladungspakete vier Umspannungen und für die oberen die von vorne bekannten sechs. Auch hier gilt wieder: Stehende I-Träger lassen sich viel leichter durch Gurte, Ketten oder Drahtseile als Block sichern. Hier muss aufgrund der Gefahr des Abrutschens jeder I-Trägerstapel mehr oder weniger einzeln gesichert werden.
Es gibt nun noch Experten, die werden uns entgegenhalten, dass zumindest die unteren I-Trägerpakete nicht mehr zusätzlich durch Umspannung gesichert werden müssen, da die oberen Pakete die unteren beschweren und aufgrund ihrer Direktsicherung über ihr gewicht sprich Masse mehr oder weniger als Niederzurrung wirken. Tatsächlich machen sie die untere Ladung schwerer und wahrscheinlich (man müsste schichtweise durch die Ladung rechnen) hätte derjenige sogar recht. Fakt ist aber, dass das zweite Paket von links davon unberücksichtigt wird und sich durch eine unglaublich aufwendige Rechnung nur drei Umspannungen sparen ließen, die man bei entsprechender Vorbereitung in wenigen Minuten gesetzt hätte.
Sicher geht eben doch am besten!!
Zurück zum Anfang