Photo of the month – July 2024 |
[German version] |
A listless fire extinguisher?
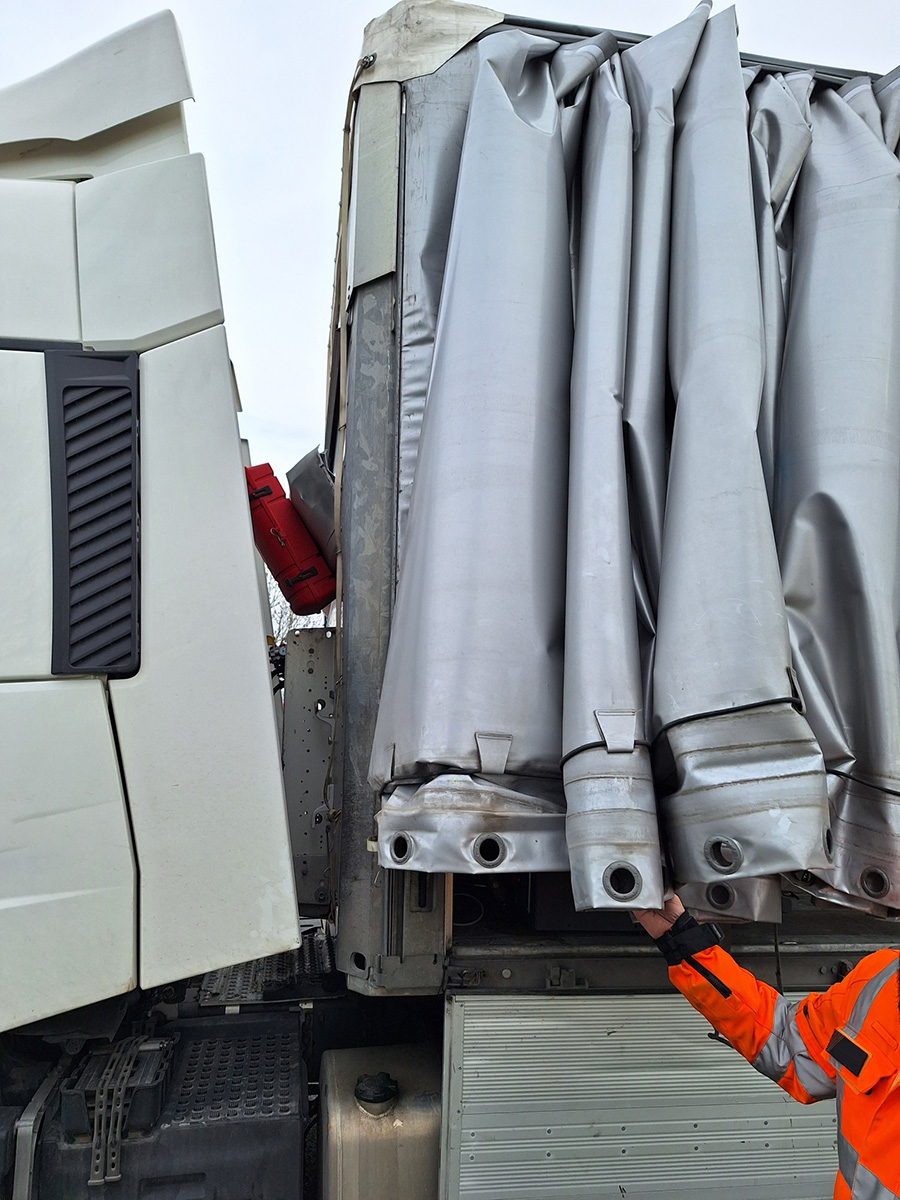
Figure 1 [Raymond Lausberg]
This fire extinguisher, which was simply “dangling” listlessly from the vehicle, aroused the interest of the Belgian police. It was only natural for them to wonder why it was just hanging there.
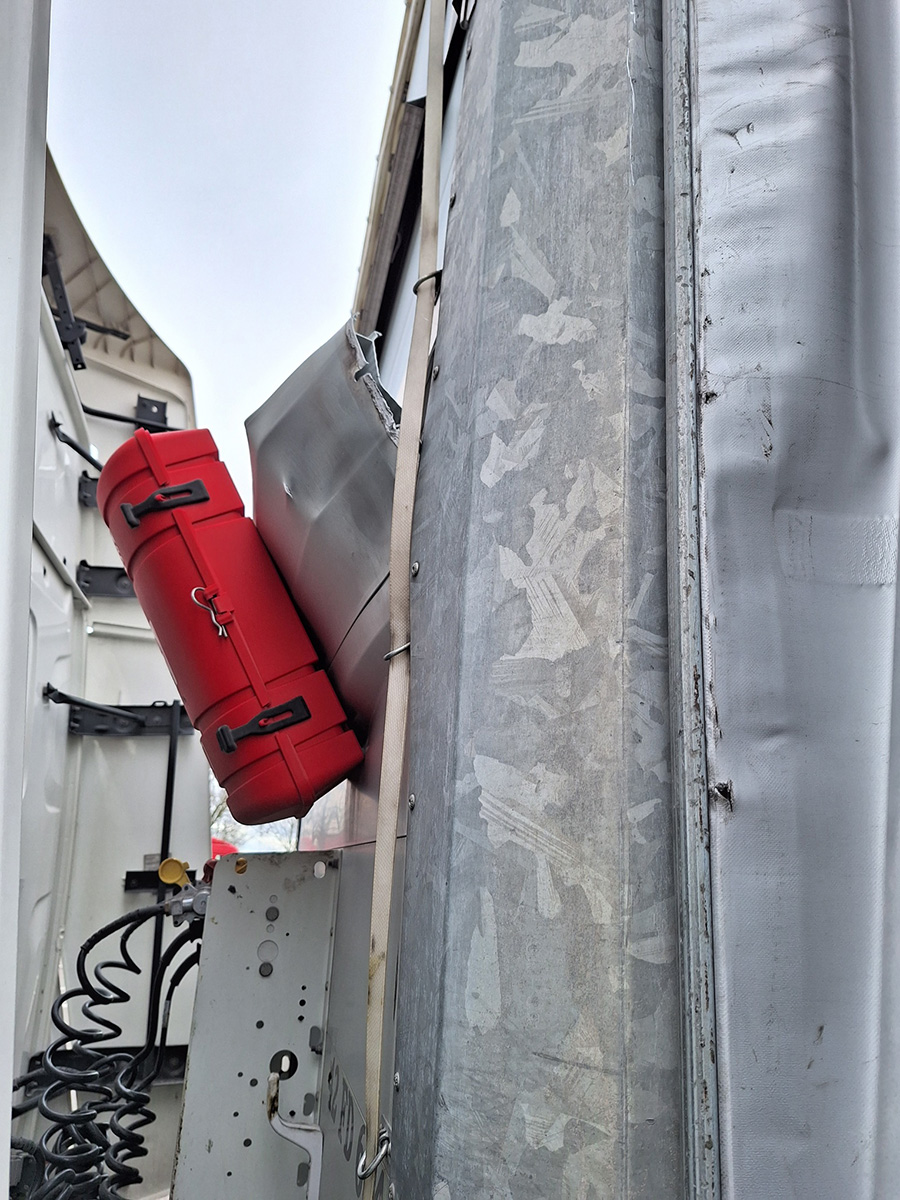
Figure 2 [Raymond Lausberg]
When they got a bit closer, all became clear. It wasn’t that the fire extinguisher was listless but that the end wall had obviously taken quite a knock. This signaled the start of a long stoppage for the vehicle.
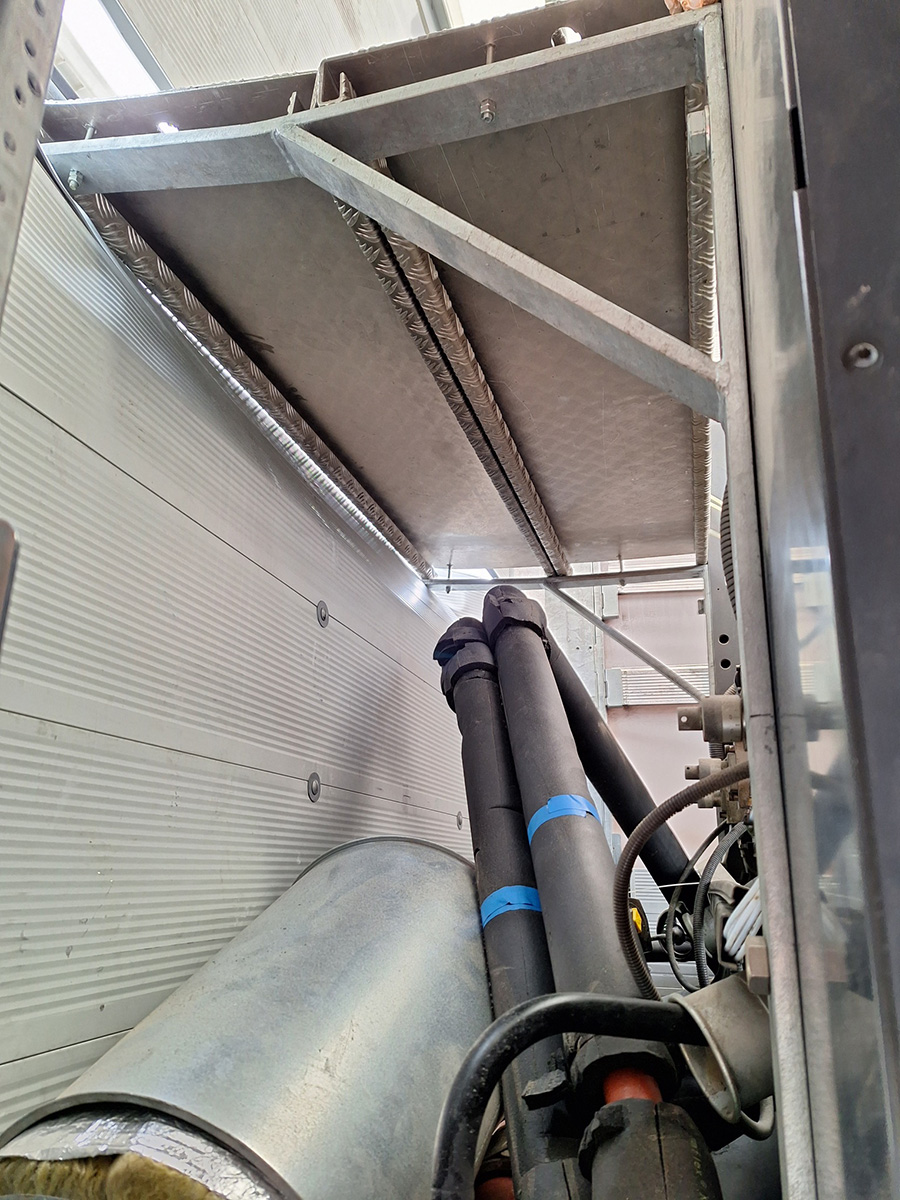
Figure 3 [Raymond Lausberg]
The load had got it into its head to dent the end wall a little from the inside out. This is the point where our ears and eyes really perked up and we wanted to find out what had happened inside on the loading bed.
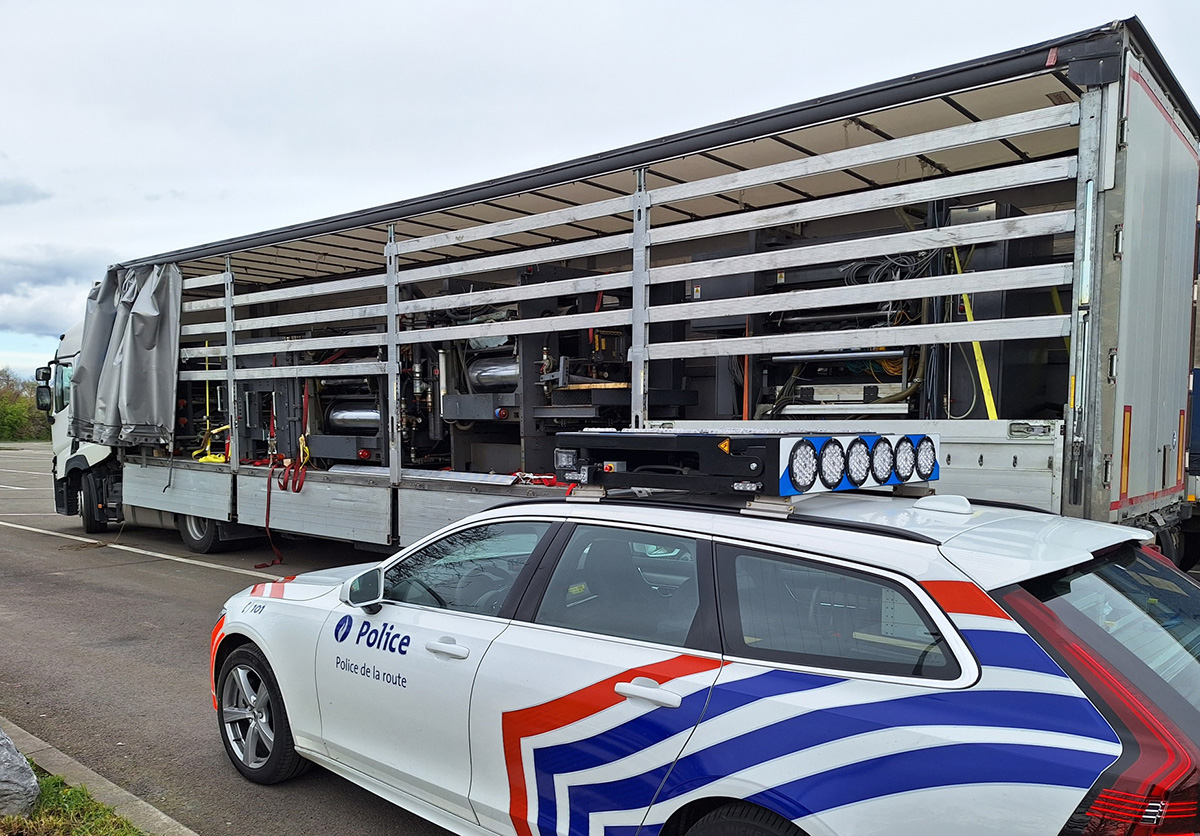
Figure 4 [Raymond Lausberg]
Four second-hand printing presses weighing a total of almost 22 tonnes. The securing equipment was simply there to look good. It consisted of tie-down lashings, although the term “lashing” is a great exaggeration. In the following short video, it is easy to see just how loose these so-called lashings were.
Video 1 [Raymond Lausberg]
Of course, we have to remember that all the machines have slipped forward a fair distance. In response to our query, we were told that most of the belts were merely decorative, that is to say they were simply hanging there without any function because they could not be pretensioned in any way without damaging sensitive parts of the printing presses
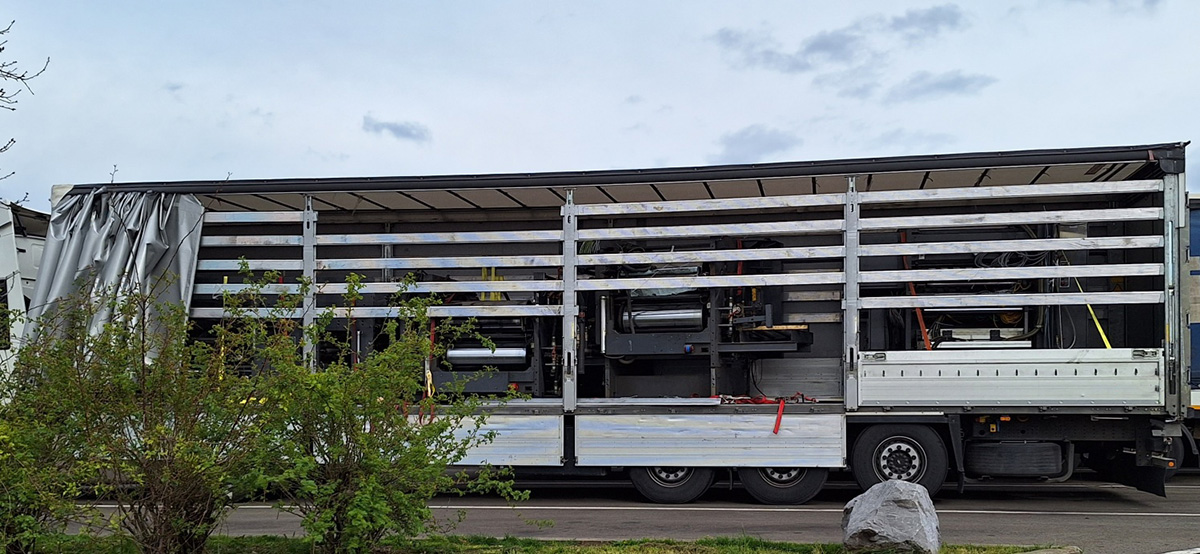
Figure 5 [Raymond Lausberg]
Only the rearmost machine (Figure 5) gives us an idea of how far it has slipped because the belts still have some degree of pretensioning and now slope diagonally.
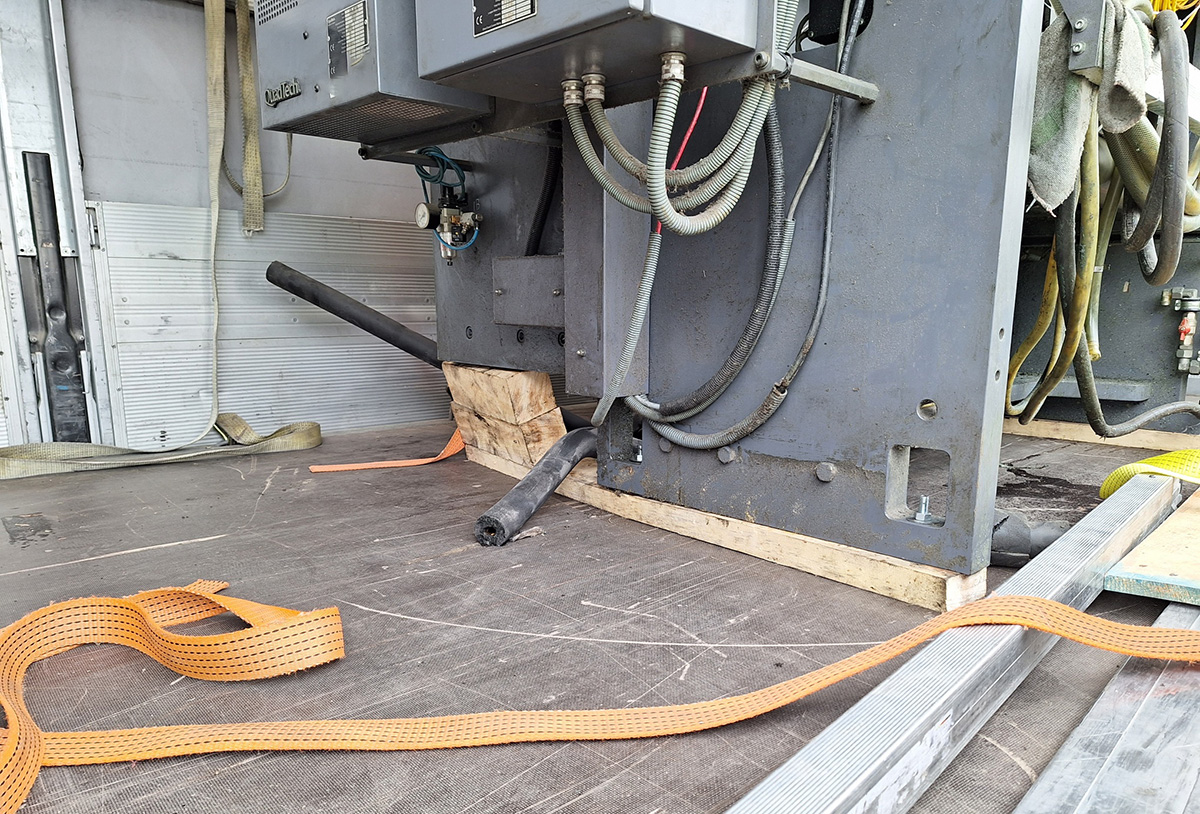
Figure 6 [Raymond Lausberg]
The way the dunnage has twisted also testifies to the movement of the load. It can easily be seen that no anti-slip material was used and so the “attempt” to secure the load was utterly pointless.
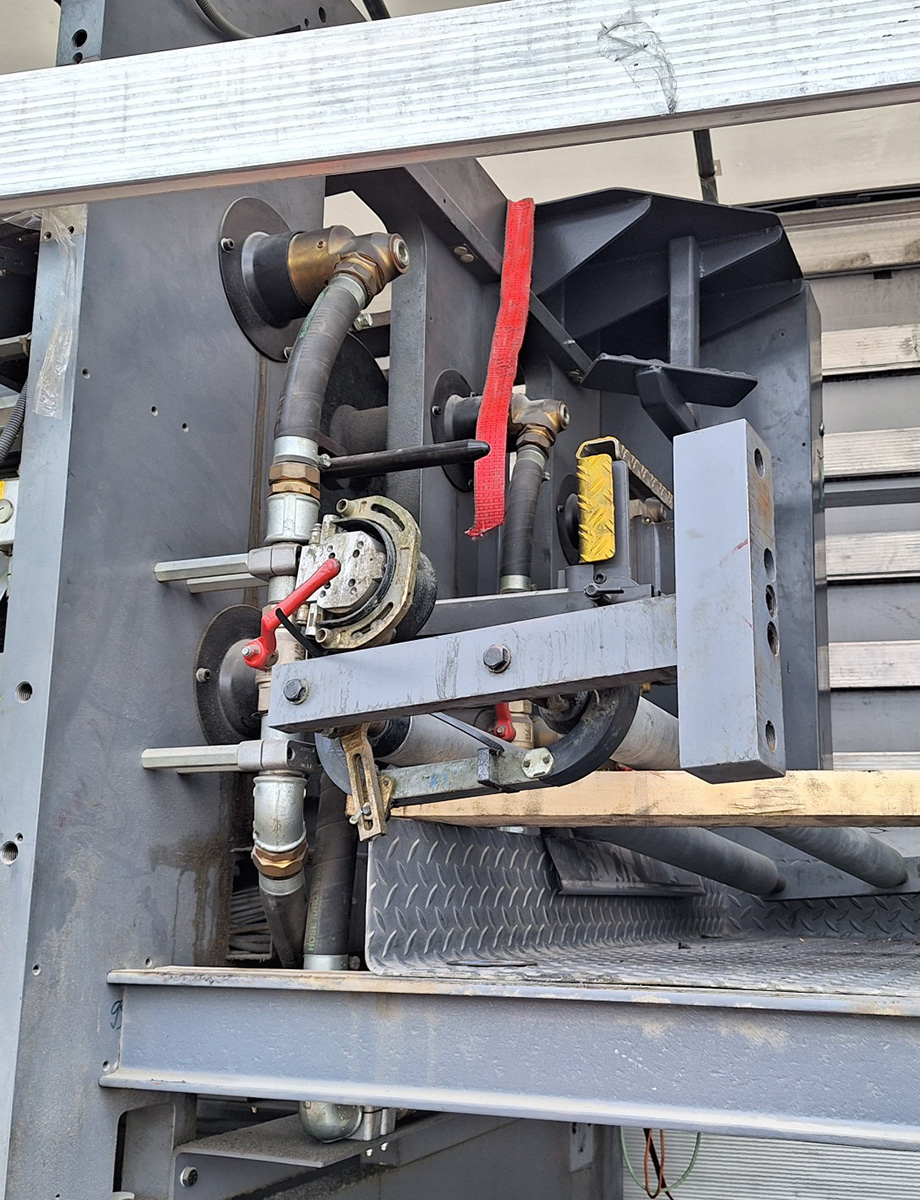
Figure 7 [Raymond Lausberg]
Two belts were attached in such a way that they were laid over sharp edges. When the load slipped, the belts were tensioned and, as is clear from this photo, were “sliced through” as if by a knife. The only way to describe this loading arrangement is catastrophic. No attention was paid to load securing and the measures that were taken were completely wrong and almost entirely useless.
Securing the load:
The total weight of the load amounted to almost 22 tonnes. For simplicity’s sake, we will distribute the weight equally across the four machines. Each of them therefore weighs 5.5 tonnes and should be secured with a force of 4,400 daN in the direction of travel.
Let us think through the two load securing options: tie-down lashings and direct lashings.
- Tie-down lashings:
We will naturally use anti-slip material that is suitable for heavy loads because the load-bearing areas are rather small and the pressure is therefore high. If the right anti-slip mats are used, we still need 1,100 daN of securing force. This means that we need a vertical component of 1,834 daN in the tie-down lashing. The geometry of the printing presses provides a number of different ways of attaching tie-down lashings. What is important is that the belts are protected against the sharp edges. It is also possible to attach direct lashings that have the effect of tie-down lashings. Because it will not necessarily be possible to establish a tie-down lashing simply by throwing a belt over each machine, we will use four tie-down lashings, i.e. two on each side, so that the machines cannot twist if subjected to a load. Even though this generates considerably more securing force than is required, the geometry of the machines means that lashings of this type can be attached without difficulty and also without very much extra work. - Direct lashings:
For this variant, we again use appropriate anti-slip material. The great advantage of securing a load by friction is that the securing force acts in all directions and therefore also secures the load to the rear and sides. Direct lashings have a correspondingly large vertical component, meaning that they also provide the minimum securing force required to generate the necessary friction. However, if direct lashings are used, the top priority is once again to protect the edges of the belts, because we have already seen that two belts were cut through when the vehicle braked.
If we secure the load with direct lashings, we again decide to use an overdimensioned securing solution with four belts in order to counter the unevenness of the load securing measures, which inevitably results from the rather difficult geometry of the machines.
Your load securing columnists wish you a safe and secure summer break.
Back to beginning